摘 要: 针对金属薄板冲压成形中的皱曲缺陷,提出一种基于有限元环境的冲压皱曲缺陷仿真分析方法。该方法根据工程实际应用经验将仿真环境中的冲压件皱曲进行了量化评估,通过对应变调节方向和应变调节量的分析,掌握起皱区域的成形性状态,为金属流动调节提供支持。
冲压起皱缺陷是金属薄板成形工艺需要解决的主要问题,是影响冲压产品质量的主要因素,型面复杂的汽车覆盖件成形尤其明显,因此受到工程师和科研人员的广泛关注。
1、 皱曲仿真分析方法的关键步骤
皱曲仿真分析流程如图 1所示,在导入增量算法求解结果(包括材料、应变、位移等数据)后,关键步聚如下:1)识别皱曲缺陷,2)量化评估皱曲程度,3)分析皱曲区域的变形历史,4)构造参考线,并查看应变分布状态,5)确定金属流动调节方向,计算流动调节量。
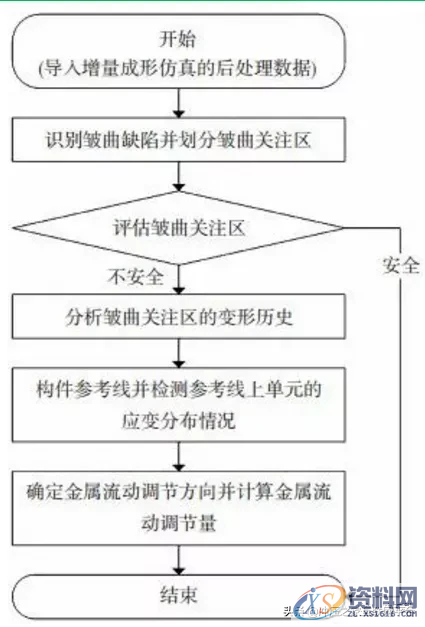
图 1 皱曲仿真分析流程
1.1 皱曲缺陷的识别
皱曲识别的目的是为后续步骤“皱曲的量化评估”做准备。式(1)~(3)确定了皱曲缺陷的识别范围。
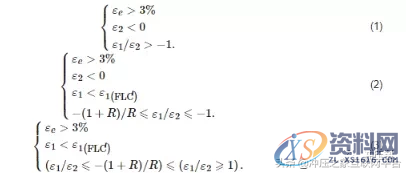
式中εe为基于Hill屈服准则的等效应变。ε1和ε2分别为主应变和次应变,ε1(FLC')为图 2中曲线FLC'上的主应变值,R为材料的平均各向异性系数。式中“εe > 3%”为了确保识别的网格单元有足够的变形量,因为在当等效应变小于3%时,属于成形不足缺陷,往往发生在冲压件的大面积、平坦区域。
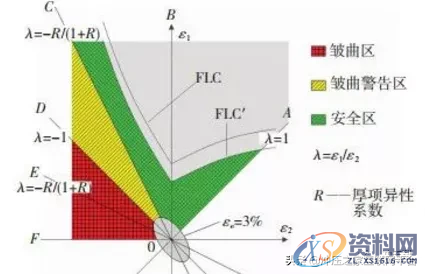
图 2 平面应变空间中的皱曲区域
式(1)定义了皱曲缺陷区,其范围如图 2中皱曲区,皱曲缺陷区内的网格单元存在两种应力状态:一种是拉-压应力状态,该应力状态下的压应力占主导,压缩变形大于拉伸变形,如图 2中“D”线到“E”线区域所示;另一种是双压应力状态,该应力状态下网格单元为压缩变形,如图 2中“E”线到“F”线区域所示。
式(2)定义了皱曲临界区,其范围如图 2中皱曲警告区,临界区内的网格单元处于拉-压应力状态下,尽管拉应力占主导,但是压应力还是可能引起皱曲,这一区域不能被忽略,因此将其作为皱曲临界区。式(3)定义了安全区,如图 2所示,该区域内的网格单元处于双拉应力状态,变形充分,是基于应变调节的目标区域。
皱曲识别后,如图 3所示,需要在零件表面区选取缺陷关注区,目的是缩小计算范围,为后续的应变调节做准备。
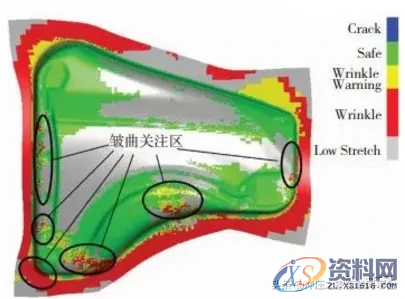
图 3 皱曲和关注区的分布
1.2 皱曲程度的量化评估
皱曲缺陷被识别后,需要对其进行量化评估,以了解皱曲的严重程度。因此,根据皱高将皱曲缺陷划分为Ⅰ、Ⅱ、Ⅲ、Ⅳ四个等级,如表 1所示,t0为板料厚度,Δhg为上模面到板料上表面之间的距离,一般为板料厚度的10%。在所有等级中,Ⅰ级皱是不能被任何汽车覆盖件产品所接受的,它属于“硬”缺陷,Ⅱ、Ⅲ、Ⅳ级属于“软”缺陷,可以被一些如车身内板零件所接受,在工程中可以降级使用,如表 2所示。

从表 2内容可知,需要测得皱曲高度,以其作为皱曲评估指数。在测量皱高时,需要考虑两种情况:一种是无约束的皱高测量,即在皱曲产生位置仅存一侧模面(上模或下模),皱曲的发展不受模面约束,如图 4(a)所示;另一种是有约束的皱高测量,即皱曲产生的位置存在两侧模面(上模和下模),皱曲发展受到上下模面的约束,如图 4(b)所示。如果是无约束皱曲,测量方法简单,只要测得皱波的波峰到模面之间的距离即可,但约束皱曲在工程中更为常见,且不易测量,因为受到模面的约束,皱波可能被压倒,此时需要追踪皱的生长历史,如图 5所示,测得皱波被压倒前的皱高作为皱曲评估指数。
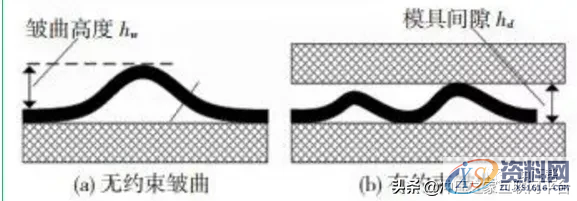
图 4 皱曲类型
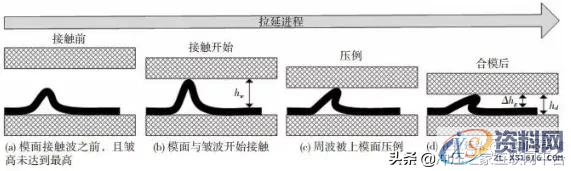
图 5 拉延过程中典型约束皱的发展过程
然而,在有限元环境中,受网格质量的影响,有时皱高的测量是不够准确的。所以需要一种方法来弥补这种不足,本文选择次应变与主应变的比值作为另一项评估指数,即图 2中λ的倒数1/λ,其代数值越小,皱曲越严重。
综上,对于一个皱曲关注区来说,最大皱高或1/λ的最小代数值可以作为皱曲评估指数,能够表征皱曲的严重程度。
1.3 皱曲区域的变形历史分析
变形历史分析的目的是获悉拉延成形过程中皱曲区域的应力状态变化,以及金属流动情况,为控制金属流动、调节应变做准备。变形历史是指应变历史,有平面应变历史和等效应变历史两种,如图 6所示。
平面应变历史反映拉延成形过程中皱曲区的应力状态,而等效应变历史则反映拉延成形过程中皱曲区金属流动特征。如图 6(a)所示,“路径1”为某单元的平面应变路径,由该单元在不同拉延阶段的平面应变空间内的应变点拟合而成,图中A、B(主应变轴)、C、D、E、F(次应变轴)6条线将平面应变空间分割为12个区域,其中AB、BC、CD、DE、EF为有效成形区域,分别对应不同的应力状态,如表 3所示。
结合图表内容,可知沿逆时针方向,AB到EF区域的应力状态由双拉应力转变为双压应力状态,所以,通过分析皱曲单元的应变历史可获悉其拉延过程中的应力变化情况。
类似地,图 6(b)中的“路径2”所示为等效应变历史曲线,通过分析“路径2”的形状可了解变形单元附近的金属流动情况,例如“路径2”大部分经过“G区”,说明变形发生较早,大部分变形在拉延初期完成,而在拉延初期,模面与板料刚刚接触,力的传递基本不受限制,金属流动属于整体性的大范围流动;当“路径2”主要落在“L区”时,则说明变形发生较晚,主要变形在拉延后期完成,在此阶段中,模面与板料已经有较多位置和较大面积的接触,力的传递会受到限制,比如在一些曲率较大位置,板料的流动将受到限制,因此这个阶段的金属流动属于局部性的小范围流动;而当“路径2”主要落在“P区”时,则说明变形是随着拉延进程逐步发生的,没有明显的提前或滞后,相应的金属流动特点介于前两中情况之间。
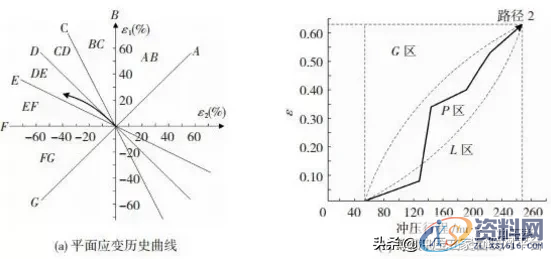
图 6 变形历史曲线
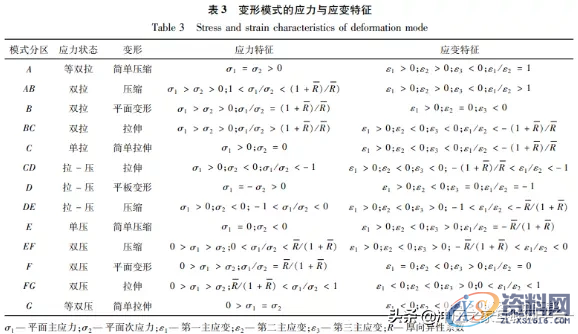
1.4 参考线的构造与应变分析
构造参考线的目的是获悉皱曲区域的应变分布状态。其构造原则为:如果皱纹明显且有规律,则参考线与皱纹垂直构建;选择主要轮廓特征线及其等距偏移线作为参考线;参考线需贯穿皱曲缺陷关注区,且经过皱曲特征点或在其附近。图 7所示为构建参考线示意图。
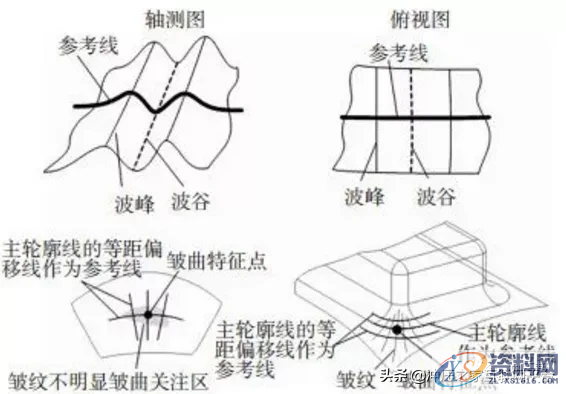
图 7 参考线构造方法
参考线构建成功后需要对其经过的网格单元进行应变分析,从而掌握皱曲缺陷区的应力情况。分析参考线上的网格单元应变有如下三种方法:
1) 主、次应变向量分布法。获取参考线经过单元的平面主应变和次应变,根据其向量分布情况分析皱曲缺陷区的受力情况。通常,皱曲越严重,皱纹越清晰,主、次应变向量的分布越规律。但是,当皱曲程度较小时,皱纹不明显,主、次应变向量分布不规律,并且主、次应变的绝对值差异不明显,该方法应用效果较差,需要使用后两种方法。
2) 平均切向、法向应变法。将参考线经过单元的主、次应变向参考线在单元处的切向和法向投影,并求得切向和法向应变平均值。
为直观地表征参考线上的平均法向和切向应变情况,采用了图 8的表现形式。椭圆的水平轴对应平均切向应变,竖直轴对应平均法向应变,椭圆越扁平说明平均切向应变相对平均法向应变越大,皱曲越严重,因为平均切向应变对应的是压应变。
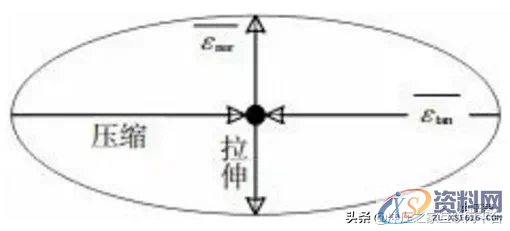
图 8 参考线上的平均法向和切向应变
3) 平面应变比值法。通过计算平面应变比值可以评估皱曲的严重程度,如图 2中的皱曲识别。按顺序将参考线经过的所有单元的平面应变比计算出来,并显示在图 9中,可以直观地反映参考线上的应变分布情况。
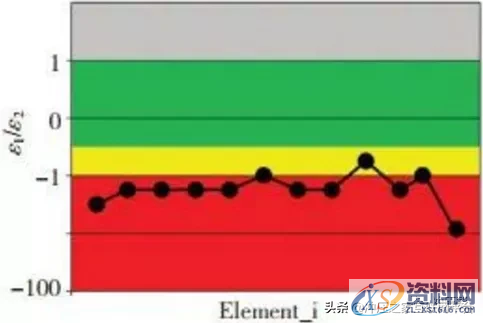
图 9 参考线上的平面应变比分布图
1.5 金属流动调节
从以上分析步骤,可以获得皱曲缺陷区的应力状态,金属流动特征,参考线经过单元的应变分布情况。从金属流动调节的角度消除皱曲缺陷,需要提供调节方向和参考量。调节方向可以作为选择工艺调整手段的参照,而调节参考量可以作为工艺参数值设置的参照。
本文提供了四种方法来确定调节方向,如图 10和图 11所示,沿参考线在特征点(皱曲最严重点/关注区中心点)处切线方向;沿特征点的次应变方向;沿特征点的主应变方向;沿垂直“C线”方向,如图 11所示。四种方法需要根据零件实际情况进行选取,需要充分考虑工艺实施的有效性和可行性,如通过拉延筋、工艺孔、板料轮廓等手段达到金属流动调节目的。
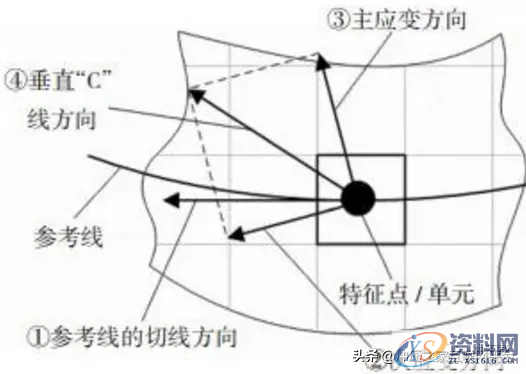
图 10 金属流动调节方向
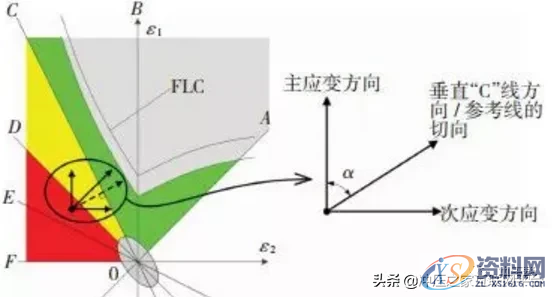
图 11 成形性图中的应变调节方向
金属流动调节方向确定后,还需要计算金属流动调节参考量,作为调整工艺参数设置参照。首先,在特征点处构建一个过调节方向和单元法向的平面;然后,求该平面与零件表面的交线,该交线就是金属流动调节线,如图 12所示;最后,计算在关注区内金属流动调节线所经过网格单元的金属流动调节参考量。如图 13所示,在调节线上的每个单元的调节量是一个范围值,即沿调节方向在“安全区”的两端,总金属流动调节参考量为所有单元调节量之和,所以也是一个范围值。
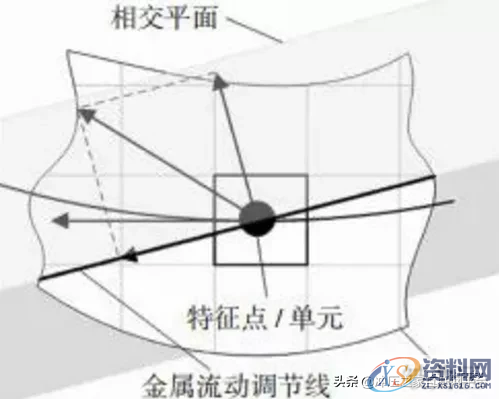
图 12 金属流动调节线

图 13 参考线上单元的最大和最小调节量
2、应用实例
为验证方法的有效性,本文选取了Numisheet 2002的标准件作为实例应用零件。先设置合适的工艺参数得到一个相对理想的仿真结果,如图 14所示,表 4-5为主要工艺参数设置情况,然后去掉图 14中的拉延筋“Db-8”,同时保证其他条件不变,此时皱曲缺陷在该位置发生,如图 15所示。
利用上文方法,首先将图 15中的皱曲缺陷区识别并对关注区进行皱曲评估,然后分析皱曲关注区特征点的变形历史(如图 16),以及参考线上的应变分布情况(如图 17),最后确定金属流动调节方向(如图 18)并计算金属流动调节量(如表 6)。
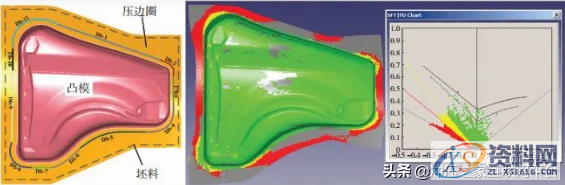
图 14 安全的成形性状态


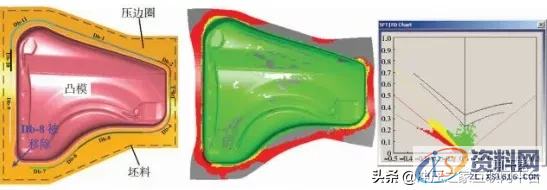
图 15 移除拉延筋后的皱曲状态
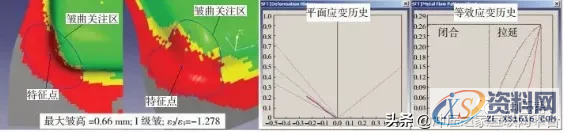
图 16 皱曲特征点分析

图 17 参考线上的应变分布
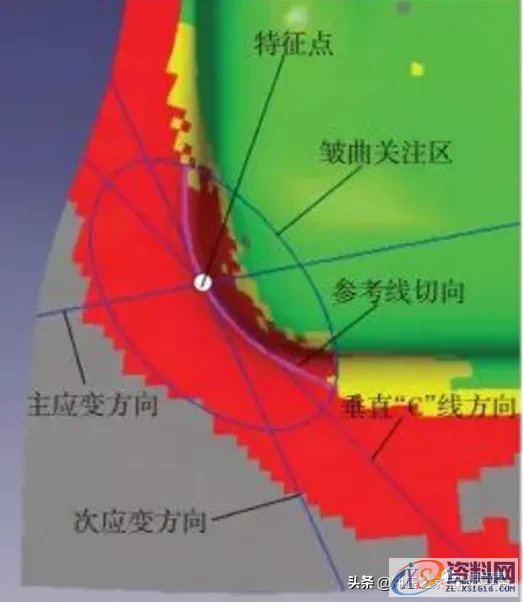
图 18 变形历史曲线
虽然图 18中给出4个调节方向,但从工艺的可实施性、调节效率和成本的角度考虑,不是每个调节方向都具有可行性的,在一些形状复杂的冲压件中,还需要考虑工艺调节方案对缺陷相邻区域变形的影响。在本例中,皱曲缺陷发生在圆角处,仅沿主应变方向调节容易实现,可通过设置图 14中的拉延筋Db-8来实现,表 6为逐步增加拉延筋Db-8阻力和举力所对应的金属流动调节量。
从表 6中可以看到,金属流动调节量随拉延筋Db-8的阻力和举力的增大而减少,当拉延筋Db-8增加到合适的阻力和举力时,金属流动调节量趋近于0,即皱曲消除,证明了本文方法的有效性。
3 、结论
通过以上的方法和应用研究,得到以下结论:
1) 本文提出的消除皱曲缺陷的仿真分析方法是有效、可行的;
1;所有标注为智造资料网zl.fbzzw.cn的内容均为本站所有,版权均属本站所有,若您需要引用、转载,必须注明来源及原文链接即可,如涉及大面积转载,请来信告知,获取《授权协议》。
2;本网站图片,文字之类版权申明,因为网站可以由注册用户自行上传图片或文字,本网站无法鉴别所上传图片或文字的知识版权,如果侵犯,请及时通知我们,本网站将在第一时间及时删除,相关侵权责任均由相应上传用户自行承担。
内容投诉
智造资料网打造智能制造3D图纸下载,在线视频,软件下载,在线问答综合平台 » 冲压起皱缺陷的仿真分析方法