第九章 浇注系统及排气设计
9.1 浇注系统设计原则
9.1.1 浇注系统的组成
模具的浇注系统是指模具中从注塑机喷嘴开始到型腔入口为止的流动动通道,它可分为普通流道浇注系统和无流道浇注系统两大类型。普通流道浇注系统包括主流道、分流道、冷料井和浇口组成。如图
9-1所示。
9.1.2 浇注系统设计时应遵循如下原则:
1 .结合型腔的排位,应注意以下三点:
a .尽可能采用平衡式布置,以便熔融塑料能平衡地充填各型腔;
b .型腔的布置和浇口的开设部位尽可能使模具在注塑过程中受力均匀;
c .型腔的排列尽可能紧凑,减小模具外形尺寸。
2 .热量损失和压力损失要小
a .选择恰当的流道截面;
b .确定合理的流道尺寸;
在一定范围内,适当采用较大尺寸的流道系统,有助于降低流动阻力。但流道系统上的压力降较小的情况下,优先采用较小的尺寸,一方面可减小流道系统的用料,另一方面缩短冷却时间。
c .尽量减少弯折,表面粗糙度要低。
3 .浇注系统应能捕集温度较低的冷料,防止其进入型腔,影响塑件质量;
4 .注系统应能顺利地引导熔融塑料充满型腔各个角落,使型腔内气体能顺利排出;
5 .防止制品出现缺陷;
避免出现充填不足、缩痕、飞边、熔接痕位置不理想、残余应力、翘曲变形、收缩不匀等缺陷。
6 .浇口的设置力求获得最好的制品外观质量浇口的设置应避免在制品外观形成烘印、蛇纹、缩孔等缺陷。
7 .口应设置在较隐蔽的位置,且方便去除,确保浇口位置不影响外观及与周围零件发生干涉。
8 .考虑在注塑时是否能自动操作
9 .考虑制品的后续工序,如在加工、装配及管理上的需求,须将多个制品通过流道连成一体。
9.2 流道设计
9.2.1 主流道的设计
(1) 定义:
主流道是指紧接注塑机喷嘴到分流道为止的那一段流道,熔融塑料进入模具时首先经过它。一般地,要求主流道进口处的位置应尽量与模具中心重合。
(2) 设计原则:
热塑性塑料的主流道,一般由浇口套构成,它可分为两类:两板模浇口套和三板模浇口套。
参照图9-2,无论是哪一种浇口套,为了保证主流道内的凝料可顺利脱出,应满足:
D = d + (0.5 ~ 1) mm (1)
R1= R2 + (1 ~ 2) mm (2)
其它相关尺寸详见第十六章第四节。
9.2.2 冷料井的设计
(1) 定义及作用:
冷料井是为除去因喷嘴与低温模具接触而在料流前锋产生的冷料进入型腔而设置。它一般设置在主流道的末端,分流道较长时,分流道的末端也应设冷料井。
(2) 设计原则 :
一般情况下,主流道冷料井圆柱体的直径为6 ~ 12mm,其深度为6 ~ 0mm。对于大型制品,冷料井的尺寸可适当加大。对于分流道冷料井,其长度为(1 ~ 1.5)倍的流道直径。
(3) 分类:
a .底部带顶杆的冷料井
由于第一种加工方便,故常采用。Z形拉料杆不宜多个同时使用,否则不易从拉料杆上脱落浇注系统。如需使用多个Z形拉料杆,应确保缺口的朝向一致。但对于在脱模时无法作横向移动的制品,应采用第二种和第三种拉料杆。根据塑料不同的延伸率选用不同深度的倒扣d。若满足:(D-d)/D< d1,则表示冷料井可强行脱出。其中d1是塑料的延伸率。
表9-1 树脂的延伸率( % )
树脂 | PS | AS | ABS | PC | PA | POM | LDPE | HDPE | RPVC | SPVC | PP |
d1 | 0.5 | 1 | 1.5 | 1 | 2 | 2 | 5 | 3 | 1 | 10 | 2 |
b .推板推出的冷料井
这种拉料杆专用于胶件以推板或顶块脱模的模具中。拉料杆的倒扣量可参照表9-1。
锥形头拉料杆(图 9-4 c 示)靠塑料的包紧力将主流道拉住,不如球形头拉料杆和菌形拉料杆(图9-4 b、c 所示)可靠。为增加锥面的摩擦力,可采用小锥度,或增加锥面粗糙度,或用复式拉料杆(图9-d示)來替代。后两种由于尖锥的分流作用较好,常用于单腔成型带中心孔的胶件上,比如齿轮模具。
c .无拉料杆的冷料井
对于具有垂直分型面的的注射模,冷料井置于左右两半模的中心线上,当开模时分型面左右分开,制品于前锋冷料一起拔出,冷料井不必设置拉料杆。见图9-5。
d .分流道冷料井
一般采用图9-6中所示的两种形式:图a所示的将冷料井做在后模的深度方向;图b所示的将分流道在分型面上延伸成为冷料井。有关尺寸可参考图9-6。
9.2.3 分流道的设计
熔融塑料沿分流道流动时,要求它尽快的充满型腔,流动中温度降尽可能小,流动阻力尽可能低。同时,应能将塑料熔体均衡地分配到各个型腔。所以,在流道设计时,应考虑:
(1) 流道截面形状的选用
较大的截面面积,有利于减少流道的流动阻力;较小的截面周长,有利于减少熔融塑料的热量散失。我们称周长与截面面积的比值为比表面积(即流道表面积与其体积的比值),用它来衡量流道的流动效率。即比表面积越小,流动效率越高。
表9-2 不同截面形状分流道的流动效率及散热性能
| 名称 | 圆 形 | 正六边形 | U 形 | 正方形 | 梯 形 | 半圆形 | 矩 形 | ||
流道截面 | 图形及尺寸代号 | | ||||||||
效率 (P=S/L)值 | 通用表达式 |
|
|
|
|
|
|
| b/2 | 0.167b |
b/4 | 0.100b | |||||||||
b/6 | 0.071b | |||||||||
截面面积S =πR2时的P值 | | |
|
|
|
|
| b/2 | 0.209D | |
b/4 | 0.177D | |||||||||
b/6 | 0.155D | |||||||||
使截面面积S =πR 2 |
|
|
|
|
|
|
| b/2 | 1.253D | |
b/4 | 1.772D | |||||||||
b/6 | 2.171D | |||||||||
热量损失 | 最小 | 小 | 较小 | 较大 | 大 | 更大 | 最大 |
从表9-2中,我们可以看出相同截面面积流道的流动效率和热量损失的排列顺序.
圆形截面的优点是:比表面积最小,热量不容易散失,阻力也小。缺点是:需同时开设在前、后模上,而且要互相吻合,故制造较困难。U形截面的流动效率低于圆形与正六边形截面,但加工容易,又比圆形和正方形截面流道容易脱模,所以,U形截面分流道具有优良的综合性能。以上两种截面形状的流道应优先采用,其次,采用梯形截面。U形截面和梯形截面两腰的斜度一般为5°-10°。
(2) 分流道的截面尺寸
分流道的截面尺寸应根据胶件的大小、壁厚、形状与所用塑料的工艺性能、注射速率及分流道的长度等因素来确定。对于我们现在常见(2.0~3.0)mm壁厚,采用的圆形分流道的直径一般在3.5~7.0mm之间变动,对于流动性能好的塑料,比如:PE、PA、PP等,当分流道很短时,可小到Φ2.5mm。对于流动性能差的塑料,比如:HPVC、PC、PMMA等,分流道较长时,直径可Φ10~Φ13mm。实验证明,对于多数塑料,分流道直径在5~6mm以下时,对流动影响最大。但在Φ8.0mm以上时,再增大其直径,对改善流动的影响已经很小了。
一般说来,为了减少流道的阻力以及实现正常的保压,要求:
a. 在流道不分支时,截面面积不应有很大的突变;
b. 流道中的最小横断面面积大于浇口处的最小截面面积。
对于三板模来讲,以上两点尤其应该引起重视。
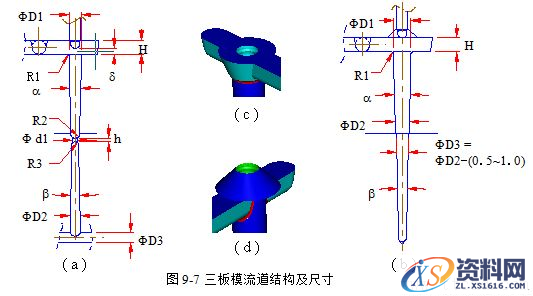
在图9-7的a图中,H 3 D1 > D2 3 D3;d1大于浇口最小截面,一般取(1.5~2.0)mm,h =d1,锥度a及b一般取2°~3°,d应尽可能大。为了减少拉料杆对流道的阻力,应将流道在拉料位置扩大,如图9-7c所示;或将拉料位置做在流道推板上,如图9-7d 所。
在图9-7的b 图中,H 3 D1,锥度a及b一般取2°~3°,锥形流道的交接处尺寸相差0.5~1.0mm,对拉料位置的要求与图9-7a 相同。
该文章所属专题:模具设计指南
9.3 浇口设计
浇口是浇注系统的关键部分,浇口的位置、类型及尺寸对胶件质量影响很大。在多数情况下,浇口是整个浇注系统中断面尺寸最小的部分(除主流道型的直接浇口外).
对于圆形流通截面,圆管两端的压力降为DP,有以下关系式:
式中 ha ------ 为熔融塑料的表观粘度
L ---- 圆形通道的长度
Q ---- 熔融塑料单位时间的流量 (cm3/sec)
R ---- 圆管半径
对于模具中常见的窄缝形流动通道,经推导有
W ---- 窄缝通道的宽度
H ---- 窄缝通道的深度
从式(9-1)和(9-2)可知,当充模速率恒定时,流动中的模具入口处的压力降DP与下列因素有关:
(1) 通道长度越长,即流道和型腔长度越长,压力损失越大;
(2) 力降和流道及型腔断面尺寸有关。流道断面尺寸越小,压力损失越大。矩形流道深度对压力降的影响比宽度影响大得多。
一般浇口的断面面积与分流道的断面面积之比约为0.03~0.09,浇口台阶长1.0~1.5mm左右。断面形状常见为矩形、圆形或半圆形。
9.3.1 浇口的类型
1.直接式浇口
优点:(1) 压力损失小;
(2) 制作简单。
缺点:(1) 浇口附近应力较大;
(2) 需人工剪除浇口(流道);
(3) 表面会留下明显浇口疤痕。
应用:(1)可用于大而深的桶形胶件,对于浅平的胶件,由于收缩及应力的原因,容易产生翘曲变形。
(2)对于外观不允许浇口痕迹的胶件,可将浇口设于胶件内表面,如图9-8c所示。这种设计方式,开模后胶件留于前模,利用二次顶出机构(图中未示出)将胶件顶出
2.侧浇口
优点:1.)形状简单,加工方便,
2.)去处浇口较容易。
缺点:1.)胶件与浇口不能自行分离,
2.)胶件易留下浇口痕迹。
参数:1.)浇口宽度W为(1.5~5.0)mm,一般取W=2H。大胶件、透明胶件可酌情加大 ;
2.)深度H为(0.5~1.5)mm。具体来说,对于常见的ABS、HIPS,常取H=(0.4~0.6)d ,其中d为胶件基本壁厚;对于流动性能较差的PC、PMMA,取 H=(0.6~0.8)d;对于POM、PA来说,这些材料流道性能好,但凝固速率也很快,收缩率较大,为了保证胶件获得充分的保压,防止出现缩痕、皱纹等缺陷,建议浇口深度H=(0.6~0.8)d;对于PE、PP等材料来说,且小浇口有利于熔体剪切变稀而降低粘度,浇口深度H=(0.4~ 0.5)d。
应用:1.)适用于各种形状的胶件,但对于细而长的桶形胶件不以采用。
3.搭接式浇口
优点:1.)它是侧浇口的演变形式,具有侧浇口的各种优点;
2.)是典型的冲击型浇口,可有效的防止塑料熔体的喷射流动。
缺点:1.)不能实现浇口和胶件的自行分离;
2.)容易留下明显的浇口疤痕。
参数:可参照侧浇口的参数来选用。
应用:适用于有表面质量要求的平板形胶件。
4.针点浇口
优点:1.)浇口位置选择自由度大,
2.)浇口能与胶件自行分离,
3.)浇口痕迹小,
4.)浇口位置附近应力小。
缺点:1.)注射压力较大,
2.)一般须采用三板模结构,结构较复杂。
参数:1.)浇口直径d一般为(0.8~1.5)mm,
2.)浇口长度L为(0.8~1.2)mm。
3.)为了便于浇口齐根拉断,应该给浇口做一锥度a,大小15°~20°左右;浇口与流道相接处圆弧R1连接,使针点浇口拉断时不致损伤胶件,R2为(1.5~2.0)mm,R3为(2.5~3.0)mm,深度h=(0.6~0.8)mm。
应用:常应用于较大的面、底壳,合理地分配浇口有助于减少流动路径的长度,获得较理想的熔接痕分布;也可用于长桶形的胶件,以改善排气。
5.扇形浇口
优点:1.)熔融塑料流经浇口时,在横向得到更加均匀的分配,降低胶件应力;
2.)减少空气进入型腔的可能,避免产生银丝、气泡等缺陷。
缺点:1.)浇口与胶件不能自行分离,
2.)胶件边缘有较长的浇口痕迹,须用工具才能将浇口加工平整。
参数:1.)常用尺寸深H为(0.25~1.60)mm,
2.)宽W为8.00mm至浇口侧型腔宽度的1/4。
3.)浇口的横断面积不应大与分流道的横断面积。
应用:常用来成型宽度较大的薄片状胶件,流动性能较差的、透明胶件。比如 PC、PMMA等。
6.潜伏式浇口(鸡嘴入水)
优点:1.)浇口位置的选择较灵活;
2.)浇口可与胶件自行分离;
3.)浇口痕迹小;
4.)两板模、三板模都可采用。
缺点:1.)浇口位置容易拖胶粉;
2.)入水位置容易产生烘印;
3.)需人工剪除胶片;
4.)从浇口位置到型腔压力损失较大。
参数:1.)浇口直径d为0.8~1.5mm,
2.)进胶方向与铅直方向的夹角a为30°~50°之间,
3.)鸡嘴的锥度b为15°~25°之间。
4.)与前模型腔的距离A为(1.0~2.0)mm。
应用:适用于外观不允许露出浇口痕迹的胶件。对于一模多腔的胶件,应保证各腔从浇口到型腔的阻力尽可能相近,避免出现滞流,以获得较好的流动平衡。
7.弧形浇口
优点:
1.)浇口和胶件可自动分离;
2.)无需对浇口位置进行另外处理:
3.)不会在胶件的外观面产生浇口痕迹。
缺点:
1.)可能在表面出现烘印;
2.)加工较复杂;
3.)设计不合理容易折断而堵塞浇口。
参数:
1.)浇口入水端直径d为(Φ0.8~Φ1.2)mm,长(1.0~1.2)mm;
2.)A值为 2.5D 左右;
3.)Φ2.5min* 是指从大端0.8D 逐渐过渡到小端Φ2.5。
应用:常用于ABS、HIPS。不适用于POM、PBT等结晶材料,也不适用于PC、PMMA等刚性好的材料,防止弧形流道被折断而堵塞浇口。
8.护耳式浇口
优点:有助于改善浇口附近的气纹。
缺点:(1) 需人工剪切浇口;
(2) 胶件边缘留下明显浇口痕迹。
参数:(1) 护耳长度A=(10~15)mm,宽度B=A/2,厚度为进口处型腔断面壁厚的7/8;浇口宽W为(1.6~3.5)mm,深度H为(1/2~2/3)的护耳厚度,浇口长(1.0~2.0)mm。
应用:常用于PC、PMMA等高透明度的塑料制成的平板形胶件。
9.圆环形浇口
优点:(1)流道系统的阻力小;
(2)可减少熔接痕的数量;
(3)有助于排气;
(4)制作简单。
缺点:(1)需人工去除浇口;
(2)会留下较明显的浇口痕迹。
参数:(1)为了便于去除浇口,浇口深度h一般为(0.4~0.6)mm;
(2) H为(2.0~2.5)mm。
应用:适用于中间带孔的胶件。
10.斜顶式弧形浇口
优点:1)不用担心弧形流道脱模时被拉断的问题;
2)浇口位置有很大的选择余地;
3)有助于排气。
缺点:1)胶件表面易产生烘印;
2)制作较复杂;
3)弧形流道跨距太长可能影响冷却水的布置。
参数:可参考侧浇口的有关参数。
应用:1)主要适用于排气不良的或流程长的壳形胶件;
2)为了减少弧形流道的阻力,推荐其截面形状选用U形截面(见图示);
3)斜顶的设计可参照“第7.7节 斜顶、摆杆机构”;
4)浇口位置应选择在胶件的拐角处或不显眼处。
9.3.2 浇口的布置
1. 避免熔接痕出现于主要外观面或影响胶件的强度
根据客户对胶件的要求,把熔接痕控制在较隐蔽及受力较小的位置。同时,避免各熔接痕在孔与孔之间连成一条线,降低胶件强度。如图9-18(a)所示,胶件上两孔形成的熔接痕连成了一条线,这将降低胶件的强度。应将浇口位置按图9-18(b)来布置。为了增加熔接牢度,可以在熔接痕的外侧开设冷料井,使前锋冷料溢出。对于大型框架型胶件,可增设辅助流道,如图9-19 所示;或增加浇口数目,如图9-20所示,以缩短熔融塑料的流程,增加熔接痕的牢度。
2. 防止长杆形胶件在注塑压力的作用下发生变形;见图9-21,在方案(a)中,型芯在单侧注塑压力的冲击下,会产生弯曲变形,从而导致胶件变形。采用方案(b),从型芯的两侧平衡的进胶,可有效地消除以上缺陷。
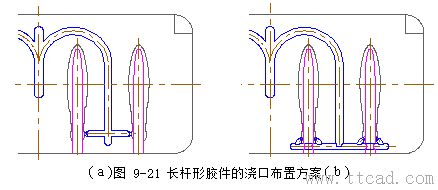
3. 避免影响零件之间的装配或在外露表面留下痕迹;如图9-22(a)所示,为了不影响装配,在按键的法兰上做一缺口,浇口位置设在缺口上,以防止装配时与相关胶件发生干涉。如图9-22(b)所示,浇口潜伏在胶件的骨位上,一来浇口位置很隐蔽,二来没有附加胶片,便与注塑时自动生产。
4. 防止出现蛇纹、烘印,应采用冲击型浇口或搭底式浇口;熔融塑料从流道经过小截面的浇口进入型腔时,
速度急剧升高,如果这时型腔里没有阻力来降低熔体速度,将产生喷射现象,如图9-23 (a)所示,轻微时在胶口附近产生烘印,严重时会产生蛇纹。如图9-23 (b)所示,若采用厚模搭底,熔融塑料将喷到前模面上而受阻,从而改变方向,降低速度,均匀地充填型腔。图9-24(a)由于熔体进入型腔时没有受到阻力,而在胶件的前端产生气纹;按9-24 (b)改进后,以上缺陷可消除。
5. 为了便於流动及保压 ,浇口应设置在胶件壁厚较厚处
6. 有利于排气
如图9-25 所示,一盖形胶件,顶部较四周薄,采用侧浇口,如图(a),将会在顶部A处形成困气,导致熔接痕或烧焦。改进办法如(b)图,给顶面适当加胶,这时仍有可能在侧面位置A产生困气;如按(c)图所示,将浇口位置设于顶面,困气现象可消除。
如图9-26所示,若按(a)图的方案进胶,预计将在位置A产生困气,建议采用方案(b),可有助于气体排出型腔。
7. 考虑取向胶件质量的影响;
对于长条形的平板胶件,浇口位置应选择在胶件的一端,使胶件在流动方向可或得一致的收缩,如图9-26(a)所示;如果胶件的流动比
较大时,可将浇口位置向中间移少量距离,如图9-26(b)所示;但不宜将浇口位置设于胶件中间,从图9-26(c)可以看出,浇口设于胶件中间时,树脂的流动呈辐射状,造成胶件的径向收缩与切线方向的收缩不匀而产生变形。
8. 对于一模多腔的模具,优先考虑按平衡式流道布置来设置浇口;如图9-28所示,建议采用(b)平衡式流道来布置浇口,有利于各型腔的平衡充填。
9. 考虑注塑生产的效率,便于流道系统与胶件的分离 模具结构确定后,应考虑流道系统和胶件便于分离,采用针点式浇口、潜伏式浇口、弧形流道可实现流道系统和胶件自动分离。选择潜伏式浇口位置时,应优先考虑在胶件本身结构上,一方面减少注塑压力,另一方面,避免生产时去除胶片。侧浇口、搭接式浇口、圆环形浇口、斜顶式浇口较易分离。直接浇口、扇形浇口、护耳式浇口则较难分离。
10.考虑加工方便
对于一模多腔的弧形流道结构,为了减少镶块的数量,应在后模将各弧形流道设置在大镶块的镶拼面上,如图9-29所示,后模由7块镶块组成,各个型腔的弧形流道在各镶块各出一半,这将简化加工工艺。
该文章所属专题:模具设计指南
9.4 流动平衡分析
流动平衡是流道系统设计时保证胶件质量的一个重要原则。从单个型腔的角度来看,它要求所有的流动路径应该同时以相同的压力充满;从多个型腔而言,每个型腔都应在同一瞬时、以相同的压力充满。
9.4.1 不平衡的流动将产生以下弊病
( 1 )先充填的区域产生过压实。
过压实可能造成以下四个方面缺陷有:
a.浪费胶料,
b.不同区域的收缩率不同将导致胶件尺寸的不一致及翘曲 ;
c.粘模、顶白;
d.过高的应力状态将缩短胶件寿命。
( 2 )增加注塑压力。可能导致:
a.先充填型腔出现飞边;
b.需要加大机器的锁模力。
( 3 )不平衡的流动往往导致分子取向的不规则,引起收缩率不一致,使胶件产生翘曲
9.4.2 实行流动平衡的方法
除了调整流道系统的尺寸以外,我们还应考虑四个因素:
( 1 )正确的浇口位置及合理的浇口数量;
该模具由大小不同的八个型腔组成,首先考虑:
a.将体积最大的型腔A布置在离主流道最近的位置;
b.且该型腔采用两点进胶。
经流动分析发现,型腔B流程较短,最早被充填满,流动秩序与其它七个型腔相差很大。
继续比较充填压力的分布。
和最高充填压力71.7Mpa相比,型腔B将承受很大的额外压力,所以,该型腔将出现过压实。
为了获得较理想的流动平衡,应给型腔B选择合理的浇口位置,并对流道系统的尺寸进一步调整,重新进行流动分析。
先考察充填时间的分析结果:
由以上分析结果可知,流道平衡得到了很好的改善。
再比较充填压力的分布:
由分析结果可知,平衡后的流道系统有效地降低了整个模具的充填压力。
( 2 )改变型腔不同部位的壁厚;
由于结构和外观的原因,浇口位置可能是确定的,如图9-33所示,浇口定在矩形盘的中心,若采用一致的壁厚2.0mm,见9-34(a)图,显然,由于浅色区域流动路径最短,它将先于深色区域被充填满,形成不平衡流动。
可以通过以下方法来实行流动平衡:
a.导流,即增加壁厚以加速流动。该例中,将深色区域的壁厚从2.0mm增加到2.5mm;
b.限流,即减少壁厚以减慢流动。该例中,将浅色区域的壁厚从2.0mm减少到1.5mm.
通过调整胶件的壁厚,使胶件获得平衡的流动秩序,如图9-33(c)。
导流和限流各有其优缺点。
导流需增加塑料用量,并要延长冷却时间,从而可能会因冷却不均匀而造成胶件翘曲。然而,这种方法可以采用较低的注塑压力以降低浇口附近的应力水平,并且能得到较好的流动平衡,最后仍会使胶件翘曲变形减小。
限流可以节约材料,且不会延长冷却时间,但会增加充填压力。
竟采用哪一种,要取决于应力和压力的大小,有时两种方法同时采用能收到更好的效果。
主要应用于大型的箱盖、面壳,以防治胶件变形,或用于解决胶件局部困气。
( 3 )对于多腔模具,合理的型腔布置;
如图9-35所示,在原型腔布置的基础上,流道系统无法实现流动平衡。因为体积较大的型腔和体积较小的型腔共用了相当长的一段流道,限制了尺寸的调节。
调整型腔布置后,对流道的布置也进行调整,可以或得较好的流动平衡。
由以上分析结果可知,调整型腔布置后,流道系统的用料并没有增加。
( 4 )尽量采用平衡式流道。
如图9-37所示,非平衡示流道布置会导致很大的流动秩序差别。
把流道系统改为平衡示布置后,可获得很好的平衡流动,见图9-38:
以上几种实现流动平衡的方法,一般优先考虑调节流道系统的尺寸来达到平衡的流动,但往往很难通过一种方法来实现,可根据实际情况选用一种,或两三种的组合。
该文章所属专题:模具设计指南
9.5 排气
模具内的气体不仅包括型腔里空气,还包括流道里的空气和塑料熔体产生的分解气体。在注塑时,这些气体都应顺利的排出。
9.5.1 排气不足的危害性:
( 1 ) 在胶件表面形成烘印、气花、接缝,使表面轮廓不清;
( 2 ) 充填困难,或局部飞边;
( 3 ) 严重时在表面产生焦痕;
( 4 ) 降低充模速度,延长成型周期。
9.5.2 排气方法
我们常用的排气方法有以下几种:
( 1 ) 开排气槽
排气槽一般开设在前模分型面熔体流动的末端,如图9-30所示,宽度b=(5~8)mm长度 L为8.0mm ~10.0mm左右。
排气槽的深度h因树脂不同而异,主要是考虑树脂的粘度及其是否容易分解。作为原则而言,粘度低的树脂,排气槽的深度要浅。容易分解的树脂,排气槽的面积要大,各种树脂的排气槽深度可参考表9-3。
表9-3 各种树脂的排气槽深度
树脂名称 | 排气槽深度(mm) | 树脂名称 | 排气槽深度(mm) |
PE | 0.02 | PA(含玻纤) | 0.03~0.04 |
PP | 0.02 | PA | 0.02 |
PS | 0.02 | PC(含玻纤) | 0.05~0.07 |
ABS | 0.03 | PC | 0.04 |
SAN | 0.03 | PBT(含玻纤) | 0.03~0.04 |
ASA | 0.03 | PBT | 0.02 |
POM | 0.02 | PMMA | 0.04 |
( 2 ) 利用分型面排气
对于具有一定粗糙度的分型面,可从分型面将气体排出。见图9-31。
( 3 ) 利用顶杆排气
胶件中间位置的困气,可加设顶针,利用顶针和型芯之间的配合间隙,或有意增加顶针之间的间隙来排气,见图9-32。
( 4 ) 利用镶拼间隙排气
对于组合式的型腔、型芯,可利用它们的镶拼间隙来排气,见图9-33、图9-34。
( 5 ) 增加走胶米仔
对于喇叭骨之类的封闭骨位,为了改善困气对流动的影响,可增加走胶米仔,米仔高出骨位h值0.50 mm左右。如图9-35所示。
( 6 ) 透气钢排气
透气钢是一种烧结合金,它是用球状颗粒合金烧结而成的材料,强度较差,但质地疏松,允许气体通过。在需排气的部位放置一块这样的合金即达到排气的目的。但底部通气孔的直径D不宜太大,以防止型腔压力将其挤压变形,如图9-36所示。由于透气钢的热传导率低,不能使其过热,否则,易产生分解物堵塞气孔。
该文章所属专题:模具设计指南
1;所有标注为智造资料网zl.fbzzw.cn的内容均为本站所有,版权均属本站所有,若您需要引用、转载,必须注明来源及原文链接即可,如涉及大面积转载,请来信告知,获取《授权协议》。
2;本网站图片,文字之类版权申明,因为网站可以由注册用户自行上传图片或文字,本网站无法鉴别所上传图片或文字的知识版权,如果侵犯,请及时通知我们,本网站将在第一时间及时删除,相关侵权责任均由相应上传用户自行承担。
内容投诉
智造资料网打造智能制造3D图纸下载,在线视频,软件下载,在线问答综合平台 » 模具设计指南-9.浇注系统及排气设计(图文教程)