开发成本降低的意义
在国产自主品牌汽车中,像奇瑞、长城、吉利、长安等主机厂每年都会开发新车型,因为自主品牌更新换代的速度太快,不像国外的大企业,一款车型能卖上百万台或是很多年;新产品的开发中会涉及到汽车模具、内外饰、电气电路、产品设计等模块的开发,往往一个新车型的开发费用就需要6 ~10 亿元。而新车型模具的开发往往就需要2.5 ~4 亿元的资金。在目前国内汽车销售市场竞争如此激烈的环境下,如果主机厂其他车型销量不多或者研发资金不充足的话,势必会影响到公司下一步的发展计划,所以在新车型的开发中降低研发成本对公司有着非常重要的意义。
模具降本的种类
模具开发成本贯穿于M0 造型阶段、车身产品结构、产品工程数据工艺设计方案及新设备新材料的应用等整个车型设计开发各阶段及环节,根据我司在以往车型模具降本方案中的经验,总共归纳出14 种降低模具吨位的方法。
CAS 阶段造型分缝检查
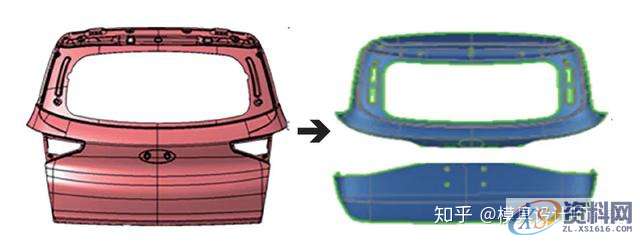
图1 零件分缝
造型分缝的原则:局部分缝线服从整体分缝线,局部特征线服从整体特征线(图1)。在车身设计过程中,车身结构的关系、冲压的难易程度都受分缝线影响,如果分缝不协调、不合理会给冲压的成形性(工艺的复杂程度)、材料利用率带来非常大的影响,由于成形性不好,原本四序模具可以生产出来的制件,就可能需要五序才能实现,大大增加了模具投入成本及后期的生产费用。
质量及量纲要求
根据公司战略纲领计划,考虑模具使用寿命(30万/50 万/100 万件),质量权衡(质量等级)相应调整模具强度及工序数,减少投资浪费(参照日系标准,如图2 所示)。
套模工艺的应用
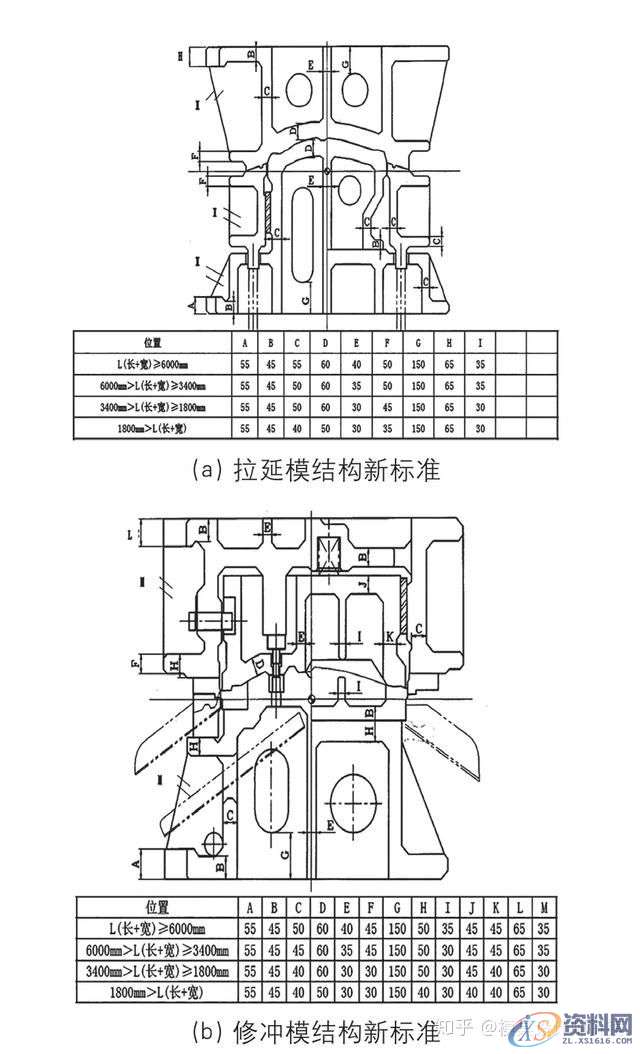
图2 新的结构标准
套模工艺使用的目的就是降低开发成本,将小件嵌套在大零件的废料区域一体成形,借助板料成形CAE 模拟技术作虚拟试模,实现模具费用、冲压费用的降低和材料利用率的提升,如图3 所示。
浅拉延方式的应用
冲压工艺设计过程中,利用压料面的随形设计,降低拉延深度,减少工艺补充,从而减小板料尺寸,可以有效提升材料利用率,同时浅拉延工艺的运用,使拉延、修冲、整形序模具的大小和吨位得到了有效的控制,从而降低了模具开发成本。
针对相对规则的产品(图4),浅拉延的工艺要点有:A、调试后板料距离拉延筋不超过10mm;B、拉延筋最小化设计且增加阻力系数,减少双筋设计;C、压料面最小化设计(压料筋中心到分模线不大于22mm);D、拉延深度最小化;E、工艺补充最小化设计。
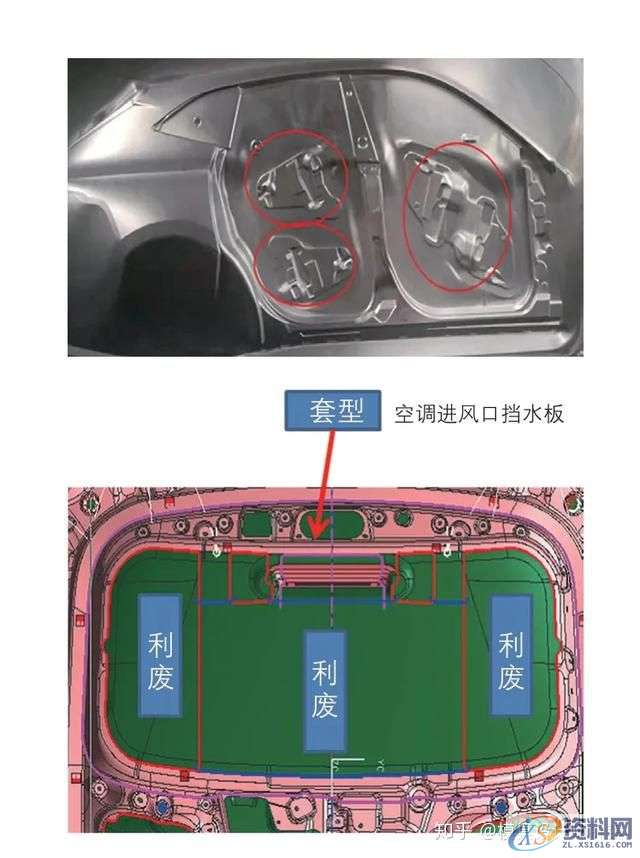
图3 套模工艺的应用
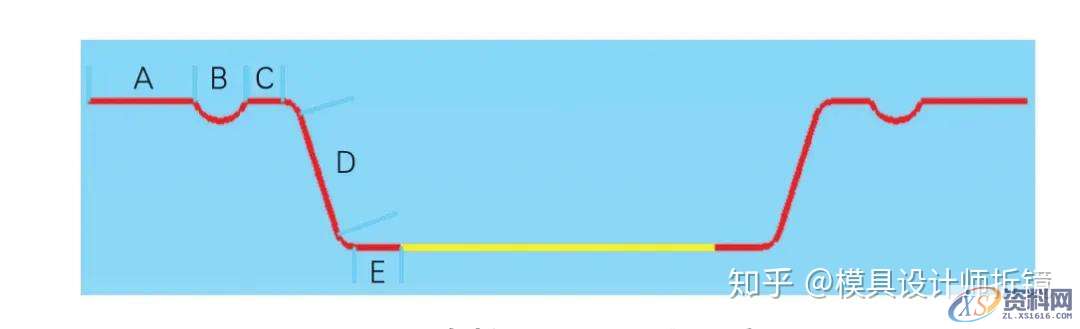
图4 浅拉延工艺要点示意
降低模具高度
在满足工艺性及设备需求下,结合生产布点排产,合理的降低模具高度,可有效降低模具开发成本。图5 所示为我司某车型车门内板优化图,通过对拉延深度、压料面角度的优化调整,减少了45mm 的拉延深度,从而减少了模具的高度,降低了开发成本。
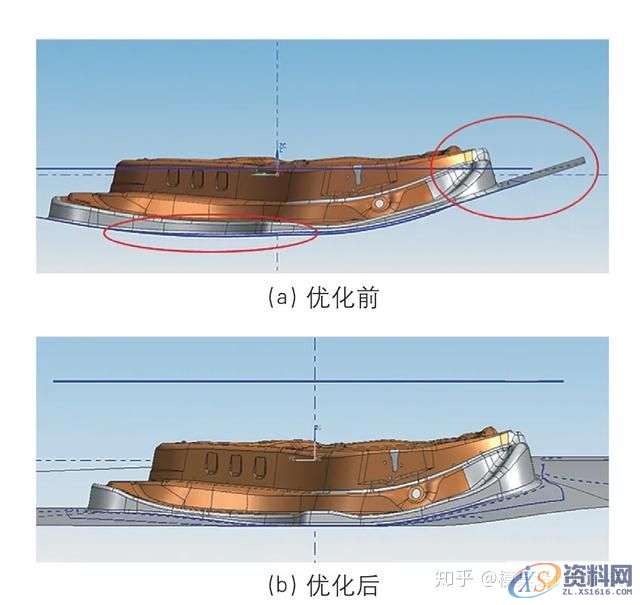
图5 优化压料面和拉延深度
合并工艺应用
合并工艺就是将两个或多个形状相同或不同的零件合并在一起同时加工,在实际生产中有意识地运用这一技巧,可以解决一些工艺问题,取得非常可观的技术经济效益。以我司某车型轮罩内板为例,轮罩内板分件(4 件)设计改为合件(2 件)设计,减少了五套模具的开发(图6),节省模具重量18 吨,一次性模具开发成本节约几十万元;钢材利用率提升22%,单车节省钢材9.284 元,制造冲次费节约5.331元/台。
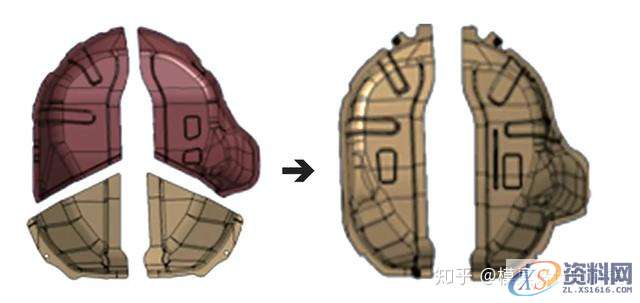
图6 轮罩内板合并工艺
成形工艺应用
传统的零件都是通过OP10 拉深模去实现零件的成形,众所周知,拉深模首先吨位大,其次在调试过程中存在一定的难度,如易产生开裂、起皱等功能性问题(图7),通过落料成形方式实现的工艺,在一定程度上避免了拉深工艺存在的问题,同时也降低了模具开发的费用(图8)。
一模多件开发
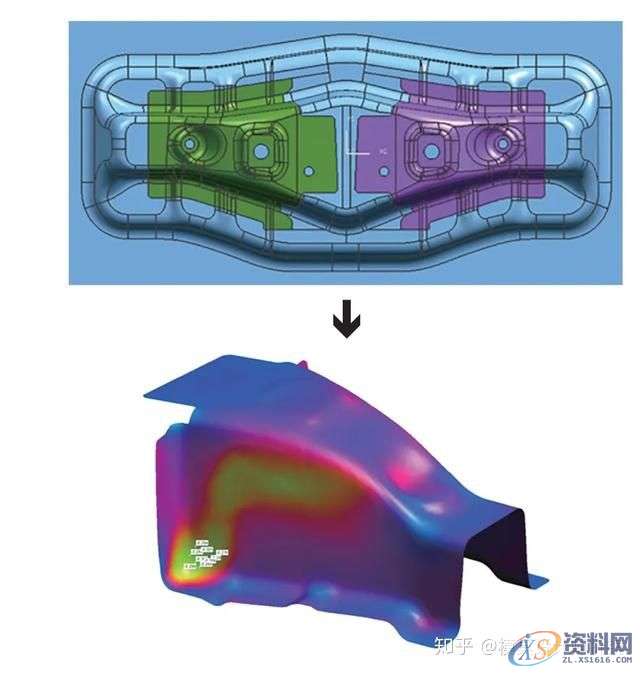
图7 通过传统拉深方式实现的零件
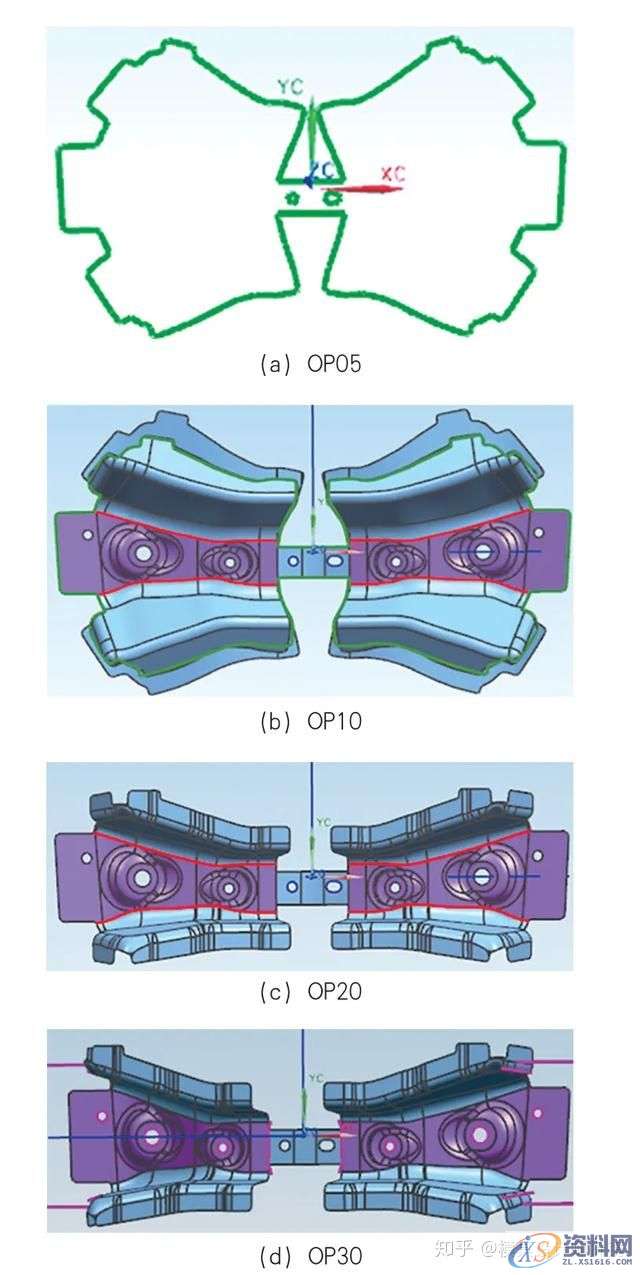
图8 通过落料方式实现的工艺
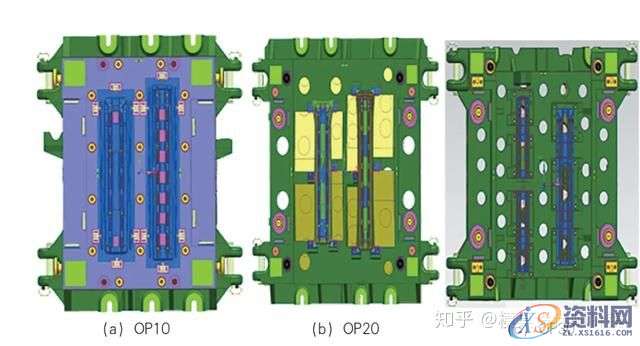
图9 一模多件开发
在一套模具中实现两种以上制件的生产,使模具开发系数(数量)降到最低。图9 所示为我司某车型左/右/前/后门外板支撑板,正常的模具工艺左/右前门外板支撑板和左/右后门外板支撑板为分开开发,此项目实现共模开发后为公司节约了模具开发成本。
工艺设计模面优化
通过CAE 软件的分析,在分模线、坯料线、拉延筋等方面进行优化,免费领取UG资料、学习视频、学历提升请联系:一三零一八六三九九七七,在保证产品质量(特别是外覆盖件的面品质量)前提下,减少零件工艺补充面、应用敞口拉延、刺破等工艺减小模具尺寸(图10),实现模具吨位降低的目的。
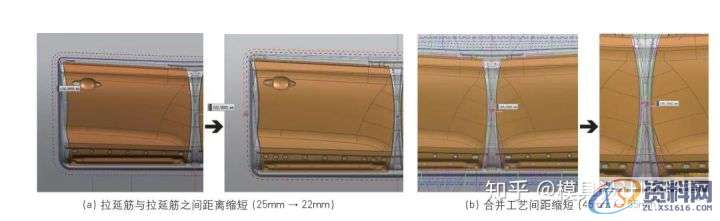
图10 模面优化
摆剪/弧形刀/锯齿刀的应用
在新车型的开发中,各主机厂为了提高整车的材料利用率,摆剪、弧形刀、锯齿刀被大量运用到实际生产中,在提高材料利用率的同时,也减小了模具的尺寸。图11 所示为我司某车型发盖内外板使用锯齿落料工艺生产的拉延件。
模具结构优化及材质替换
在模具设计阶段,结合零件外观造型可对拉深模进行结构优化,例如外覆盖件通常使用GGG70L 作为拉深模的材质,此材料采购价格较贵,通过分体式设计,模具的工作部分与非工作部分运用不同的材质(图12),可实现模具材质采购价格及模具重量降低的目的。同时,通过相关软件进行疲劳模拟,分体式结构的疲劳强度满足安全标准。
新材料的应用
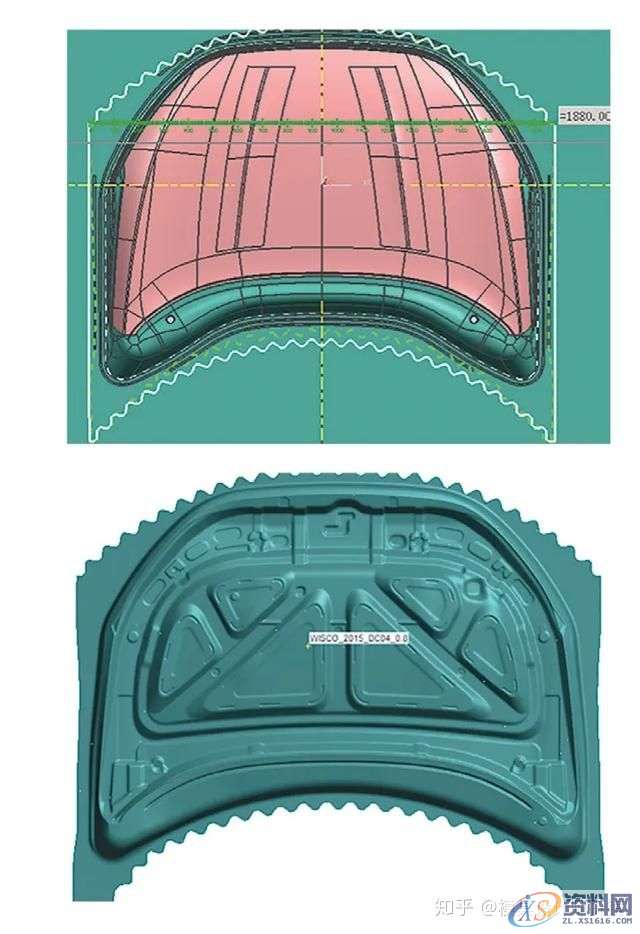
图11 锯齿刀工艺的应用
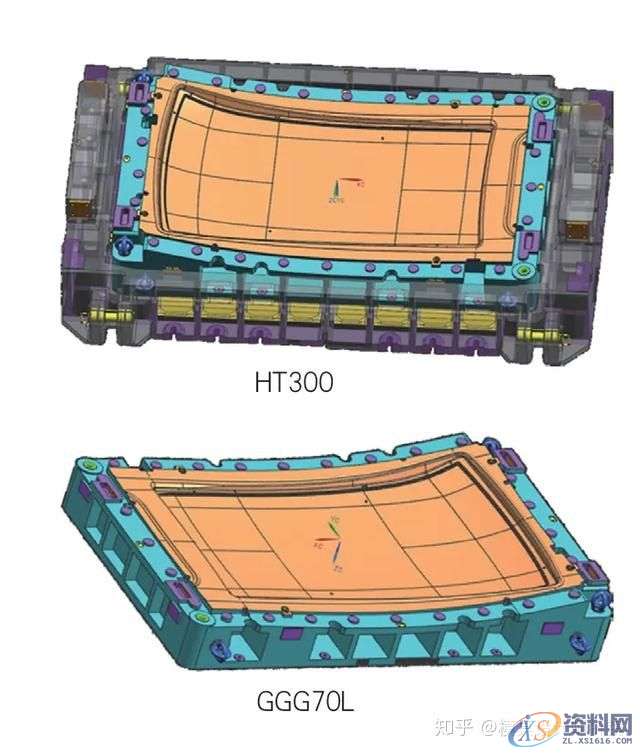
图12 分体结构设计
新材料主要是指激光拼焊板、碳纤维、高强度板,这些材料在车身上的应用除了可以降低整车的重量、降低装配误差外,还可以降低整车的制造成本,如减少外围加强件的数量、减少相应的零件数量、降低模具开发的一次性投入成本和后期的冲压费用。同时新材料的应用使车辆的抗碰撞能力、成形率和抗腐蚀能力得到了一定的提高。
新工艺的应用
热成形、辊压工艺由于具有生产效率高、节约材料、增加产品强度、质量稳定、降低开发成本等特点,被越来越多地应用到现代汽车生产制造中,提高了整车车身的安全系数。
新设备的应用
在汽车生产制造中,越来越多的新型设备被使用,如多工位压力机、单机串联、高速线的选择应用,又如多工位模具,一套模具里包含了拉深、修冲、整形等工序,一个冲次就能冲出一个成品件,大大减少了模具开发数量及冲压生产费用。
结束语
本文是结合我司常用的汽车车身模具降吨位方法进行的简单总结,在实际中可能还有其他模具降本方案没有发现。相信通过不断的研究和探讨,更多、更好的降本方法将会被发现并加以运用
东莞潇洒职业培训学校开设课程有:高升专、专升本学历提升、全日制中职学校学位、积分入户、数控编程培训、塑胶模具设计培训,压铸模具设计培训、冲压模具设计培训,精雕、ZBrush圆雕培训、Solidworks产品设计培训、pro/E产品设计培训、AutoformR7工艺分析培训,非标自动化设计、PLC编程、CNC电脑锣操机、文职培训、电商培训、平面设计等培训、电商培训,潇洒职业培训学校线下、线上等网络学习方式,随到随学,上班学习两不误,欢迎免费试学!
联系电话:13018639977(微信同号)QQ:2033825601
学校官网:www.dgxspx.com 智造人才网:www.58hr.net
学习地址:东莞市横沥镇新城工业区兴业路121号-潇洒职业培训学校
免责声明:
1;所有标注为智造资料网zl.fbzzw.cn的内容均为本站所有,版权均属本站所有,若您需要引用、转载,必须注明来源及原文链接即可,如涉及大面积转载,请来信告知,获取《授权协议》。
2;本网站图片,文字之类版权申明,因为网站可以由注册用户自行上传图片或文字,本网站无法鉴别所上传图片或文字的知识版权,如果侵犯,请及时通知我们,本网站将在第一时间及时删除,相关侵权责任均由相应上传用户自行承担。
内容投诉
智造资料网打造智能制造3D图纸下载,在线视频,软件下载,在线问答综合平台 » 降低汽车模具开发成本的方法案例
1;所有标注为智造资料网zl.fbzzw.cn的内容均为本站所有,版权均属本站所有,若您需要引用、转载,必须注明来源及原文链接即可,如涉及大面积转载,请来信告知,获取《授权协议》。
2;本网站图片,文字之类版权申明,因为网站可以由注册用户自行上传图片或文字,本网站无法鉴别所上传图片或文字的知识版权,如果侵犯,请及时通知我们,本网站将在第一时间及时删除,相关侵权责任均由相应上传用户自行承担。
内容投诉
智造资料网打造智能制造3D图纸下载,在线视频,软件下载,在线问答综合平台 » 降低汽车模具开发成本的方法案例