砂型铸造原料来源丰富,生产批量和铸件尺寸不受限制、成本低廉,是最常用的铸造方法,砂型铸件目前约占铸件总产量的90%。
一、砂型铸造的工艺过程
砂型铸造的工艺过程如下图所示。
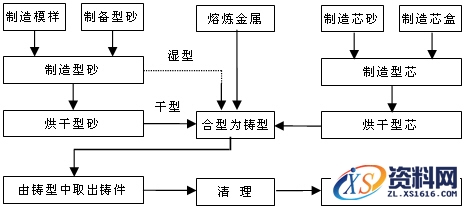
下图为砂型铸造生产套筒铸件的工艺流程示意图。
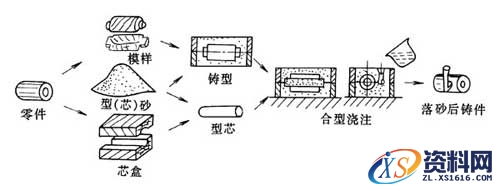
二、模样和芯盒
模样是用来形成铸型型腔的工艺装备,按组合形式,可分为整体模和分开模。芯盒是制造砂芯或其他种类耐火材料芯所用的装备。
模样和芯盒由木材、金属或其他材料制成。木模样具有质轻、价廉和易于加工等优点,但强度和硬度较低,易变形和损坏,常用于单件小批量生产。金属模样强度高,尺寸精确,表面光洁,寿命长,但制造较困难,生产周期长,成本高,常用于机器造型和大批量生产。芯盒是制造砂芯或其他种类耐火材料芯所用的装备。
三、造型材料
制造铸型或型芯用的材料,称为造型材料。一般指砂型铸造用的材料,包括砂、有机或无机粘结剂、水和其他附加物。型砂有原砂、粘结剂、附加物、旧砂和水组成。合理选用和配制造型材料,对提高铸件质量,降低成本具有重要意义。(铸型是指用型砂、金属或其他耐火材料制成,包括形成铸件形状的空腔、型芯和浇冒口系统的组合整体。)
造型材料应具有良好的流动性,以便于造出轮廓完整、清晰而准确的砂型(芯);足够的强度,可保证铸型在制造、搬运及浇注时,不致变形或毁坏;良好的透气性,可保证气体及时从液态金属中排出,避免铸件产生气孔缺陷;高的耐火度,可保证型砂在高温液态金属作用下不熔化,避免铸件产生粘砂缺陷。
四、造型和制芯
造型是指用型砂、模样、砂箱等工艺装备制造砂型的过程。制芯是将芯砂制成符合芯盒形状的砂芯的过程。
1 造型
1)手工造型
手工造型是全部用手工或手动工具完成的造型工序,主要有以下几种方法:
(1)整体模造型
特点:模样为一整体,分型面为一平面,型腔在同一砂箱中,不会产生错型缺陷,操作简单。
应用:最大截面在端都且为一平面的铸件,应用较广。
(2)分块模造型
特点:模样在最大截面处分开,型腔位于上、下型中,操作较简单。
应用:最大截面在中部的铸件,常用于回转体类等铸件。
(3)挖砂造型
特点:整体模样,分型面为一曲面,需挖去阻碍起模的型砂才能取出模样,对工人的操作技能要求高,生产工具率低。
应用:适宜中小型、分型面不平的确铸件单件、小批生产。
(4)假箱造型
特点:将模型置于预先做成好的假箱或成型底板上,可直接造出曲面分型面,代替挖砂造型,操作较简单。
应用:用于小批或成批生产,分型面不平的铸件。
(5)活块造型
特点:将模样上阻碍起爆模的部分做成活动的,取出模样主体部分后,小心将活块取出。
应用:造型较复杂,用于单件小批生产,带有凸台,难以起模的铸件。
(6)刮板造型
特点:刮板形状和铸件截面相适应,代替实体模样,可省去制摸的工序。
应用:单件小批生产,大、中型轮类、管类铸件。
(7)三箱造型
特点:采用上、下、中三个砂箱,有两个分型面,铸件的中间截面小,用两个砂箱时取不出模样,必须分模,操作复杂。
应用:单件小批生产,适合于中间截面小,两端截面大的铸件。
(8)地坑造型
特点:节省下砂箱,但造型费工。
应用:单件生产,大、中型铸件。平板的地坑造型过程
2)机器造型
机器造型是用机器全部完成或至少完成紧砂操作的造型工序。机器造型生产率高,质量稳定,劳动条件好,在大批量生产中已代替大部分手工造型。机器造型有震实造型、压实造型、震压造型、抛砂造型、射砂造型等。以震压造型最常用,见右图。
(1)制芯
芯的主要作用是形成铸件的内腔或局部外形。单件、小批生产时采用手工制芯,大批生产时采用机器制芯。手工制芯常采用芯盒制芯。为提高芯的强度可在制芯时放人铁丝或铸铁棒作为芯骨;为提高芯的透气能力,可用针扎出通气孔或埋入蜡线形成通气孔。
(2)浇注系统
浇注系统是为填充型腔和冒口而开设于铸型中的一系列通道。通常有浇口杯、直浇道、横浇道、内浇道和冒口组成,见右图。其作用是承接和导入金属液,控制金属液流动方向和速度,使金属液平稳地充满型腔;调节铸件各部分的温度分布;阻挡夹杂物进入型腔。
浇注系统按熔融金属导入铸型的位置分为以下三种:
顶注式浇注系统是从铸型顶部导入熔融金属,其特点是补缩作用好、金属液消耗少,但金属液对铸型的冲击大,易产生砂眼、冷豆等缺陷。适用于形状简单、高度小的铸件。
底注式浇注系统是从铸型底部导入熔融金属,其特点是金属液对铸型的冲击小,有利于排气、排渣,但不利于补缩,易产生浇不到缺陷。适用于大、中型尺寸,壁部较厚、高度较大、形状复杂的铸件。
阶梯式浇注系统在铸型的高度方向上,从底部开始,逐层在不同高度上导入熔融金属,具有顶注式和底注式的优点,主要用于高大和形状较复杂的薄壁铸件。
浇注系统按各浇道横截面积的关系,分为封闭式和开放式两种。
封闭式浇注系统的直浇道出口横截面积大于横浇道截面积,横浇道出口横截面积又大于内浇道截面积,其特点是金属液易于充满各通道,挡渣作用好,但对铸型的冲击力大。一般适用于灰铸铁件。
开放式浇注系统正好相反,金属液能较快地充满铸型,冲击小,但挡渣效果差,一般用于薄壁和尺寸较大的铸件。
(3)冒口和铸型结构
尺寸较大的铸件或体收缩率较大的金属还要加设冒口起补缩作用,为便于补缩,冒口一般设在铸件的厚部或上部。冒口还可起排气和集渣作用。
将铸型的各组元(上型、下型、芯、浇口杯等)组合成一个完整铸型的过程称为合型。右图是两箱造型合型后的铸型结构。合型时应检查铸型内腔是否清洁,芯是否完好无损;芯的安放要准确、牢固,防止偏芯;砂箱的定位应当准确,以防错型。
五、铸铁的熔炼和浇注
1)铸铁的熔炼
铸铁熔炼不仅仅是单纯的熔化,还包括冶炼过程,使浇进铸型的铁液,在温度、化学成分和纯净度方面都符合预期要求。
冲天炉熔炼是目前常用且经济的熔炼方法。冲天炉炉料主要有金属料、燃料和熔剂三部分。金属料一般采用高炉生铁、回炉料、废钢和铁合金;燃料采用焦炭;熔剂采用石灰石和萤石,其主要作用是造渣。
电炉熔炼能准确调整铸铁液成分、温度,能保证铸件的质量,适合于过热和精炼,但耗电量大。冲天炉—感应电炉双联熔炼是采用冲天炉熔化铸铁,利用电炉进行过热、保温、储存、精炼,以确保铸铁液的质量。
2)浇注
浇注是指将熔融金属从浇包中浇入铸型的操作。为保证铸件质量,应对浇注温度和速度加以控制。
铸铁的浇注温度为液相线以上200℃(一般为1250~1470℃)。若浇注温度过高,金属液吸气多、体收缩大,铸件容易产生气孔、缩孔、粘砂等缺陷;若浇注温度过低,金属液流动性差,铸件易产生浇不到、冷隔等缺陷。
浇注速度过快会使铸型中的气体来不及排出而产生气孔,并易造成冲砂;浇注速度过慢,使型腔表面烘烤时间长,导致砂层翘起脱落,易产生夹砂结疤、夹砂等缺陷。 (返回TOP)
六、落砂、清理与检验
落砂是指用手工或机械方法使铸件与型(芯)砂分离的操作。落砂应在铸件充分冷却后进行,若落砂过早,铸件的冷速过快,会使灰铸铁表层出现白口组织,导致切削困难;若落砂过晚,由于收缩应力大,会使铸件产生裂纹,且影响生产率,因此浇注后应及时进行落砂。
清理是指对落砂后的铸件清除表面粘砂、型砂、多余金属(包括浇冒口、飞翅和氧化皮)等过程。
铸后应对铸件进行检验,并将合格铸件进行去应力退火。
七、合金的铸造性能简介
金属的铸造性能是指铸造成形过程中获得外形准确、内部健全铸件的能力。主要有流动性、收缩性、偏析、吸气性、氧化性等。
1)流动性
(1)流动性对铸件质量的影响
流动性是指金属液本身的流动能力,直接影响到金属液的充型能力。流动性好的金属,充型能力强,能铸出形状复杂、轮廓清晰、尺寸精确、薄壁的铸件,避免出现冷隔、浇不到等缺陷;有利于金属液中夹杂物和气体的上浮与排除,减少气孔、夹渣等缺陷;有利于发挥冒口的补缩作用,防止铸件产生缩孔、缩松缺陷。
2)影响流动性的因素
(1)化学成分
共晶成分的合金流动性好,合金的成分越远离共晶点,结晶温度范围越宽,其流动性越差。在常用铸造合金中,灰铸铁的流动性最好,铝合金次之,铸钢最差。
(2)浇注工艺条件
提高浇注温度可改善金属的流动性。但浇注温度过高,会使收缩量增大、铸件易产生粘砂等缺陷;提高浇注压力,可适当提高金属液的流速,流动性好,充型能力强。
(3)铸型
铸型材料的导热性对金属液充型能力影响较大,导热性越好,充型能力越差;铸型内腔的形状和尺寸对充型能力也有影响,形状越复杂,壁越薄,金属液充型能力越差。
2)收缩
收缩是铸造合金从液态凝固和冷却至室温过程中产生的体积和尺寸的缩减。包括液态收缩、凝固收缩和固态收缩三个阶段。
(1)收缩对铸件质量的影响
液态收缩和凝固收缩表现为合金的体积变化,它是铸件产生缩孔和缩松的主要原因;固态收缩是铸件产生铸造应力、变形和开裂的基本原因。
(2)影响收缩率的因数
化学成分
铁碳合金中灰铸铁的收缩率小,铸钢的收缩率大。这是因为灰铸铁在结晶过程中析出比体积(单位质量物质的体积)大的石墨,产生的体积膨胀抵消了部分收缩。在灰铸铁中,提高碳、硅含量和减少硫含量均可减小收缩。
浇注温度
浇注温度越高,液态收缩越大,为减少收缩,浇注温度不宜过高。
铸件结构与铸型材料
型腔形状越复杂,型芯的数量越多,铸型材料的退让性越差,对铸件固态收缩的阻碍越大,产生的铸造收缩应力越大,容易产生裂纹。
八、砂型铸造工艺设计简介
铸造工艺设计是根据铸件结构特点、技术要求、生产批量、生产条件等,确定铸造方案和工艺参数,绘制图样和标注符号、编制工艺和工艺规程等。他是进行生产、管理、铸件验收和经济核算的依据。其主要内容是绘制铸造工艺图和铸件图。
1)铸造工艺图
铸造工艺图是利用各种工艺参数及符号表示铸型分型面、浇冒口系统、浇注位置、型芯结构尺寸、控制凝固措施(冷铁、保温衬板)等内容的图样。他是制造模样、模板、铸型、生产准备和验收最基本的工艺文件。
2)浇注位置的确定
浇注位置是浇注时铸件在铸型中所处的位置。浇注位置对铸件的质量影响很大,选择时应考虑以下四点所示的原则。
主要工作面和重要面应朝下或置于侧壁
a、床身的导轨面要求组织致密、耐磨,所以导轨面朝下是合理的。
b、气缸套要求质量均匀一致,浇注时应使其圆周表面处于侧壁 。
宽大平面朝下
大平面长时间受到金属液的烘烤容易掉砂,在平面上易产生夹砂、砂眼、气孔等缺陷,故铸件的大平面应尽量朝下。如上右图划线平板的平面应朝下。
薄壁面朝下
铸件薄壁处铸型型腔窄,冷速快,充型能力差,容易出现浇不到和冷隔的缺陷。如右图电机端盖薄壁部位朝小,可避免冷隔、浇不到等缺陷。
厚壁朝下
将厚大部分放于上部,可使金属液按自下而上的顺序凝固,在最后凝固部分便于采用冒口补缩,以防止缩孔的产生。如将缸头的较厚部位置于顶部,便于设置冒口补缩。
3)分型面的确定
分型面是铸型组元间的接合面,他对铸件质量、制模、制芯、合型等工序的复杂程度影响很大。确定分型面应考虑便于起模、简化铸造工艺、保证铸件质量。
(1)尽可能使铸件全部或主要部分置于同一砂箱中,以避免错型而造成尺寸偏差。
左图a不合理,铸件分别处于两个砂箱中。
左图b合理,铸件处于同一砂箱中,既便于合型,又可避免错型。
(2)尽可能使分型面为一平面
右图a若采用俯视图弯曲对称面作为分型面,则需要采用挖砂或假箱造型,使铸造工艺复杂化。
右图b起重臂按图中所示分型面为一平面可用分模造型、起模方便。
(3)尽量减少分型面
下图a槽轮部分用三箱手工造型,操作复杂。
下图b若槽轮部分用环形芯来形成,可用二箱造型,简化造型过程 ,又保证铸件质量,提高生产率。
4)工艺参数的确定
(1)加工余量及尺寸公差
加工余量是铸件加工面上,在铸造工艺设计时预先增加的,在机械加工时需切除的金属层厚度。尺寸公差是指铸件基本尺寸允许的最大极限尺寸和最小极限尺寸之差值。
①铸件加工余量确定
加工余量的大小取决于铸件材料、铸造方法、铸件尺寸与形状复杂程度、生产批量、加工面在铸型中的位置及加工面的质量要求。一般灰铸铁件的加工余量小于铸钢件,有色金属件小于灰铸铁件;手工造型、单件小批、形状复杂、大尺寸、位于铸型上部的面及质量要求高的面,加工余量大些;机器造型、大批生产加工余量可小些。但加工余量过大会浪费材料、增加机加工工时;过小又不易保证加工面的质量。
②铸件尺寸公差确定
铸件尺寸公差数值按GB6414-1986确定,在图样上的标注方法有二种:其一是采用公差等级代号标注, 其二是将公差直接在铸件基本尺寸后面标注,如“95±3.2”。
(2)起模斜度
为使模样从铸型中取出或型芯从芯盒中脱出,平行于起模方向在模样(或芯盒)壁上所增加的斜度称为起模斜度,如右图所示。
模样的起模斜度有三种取法,见下图所示。
(3)铸造收缩率
为补偿铸件在冷却过程中产生的收缩,模样比铸件图样尺寸增大的数值,主要与合金种类,也与型砂的退让性、阻碍收缩等因素有关。通常,中小型灰铸铁件线收缩率约取1%;有色金属约取l.5%;铸钢件约取2%。
(4)最小铸出孔
当铸件上的孔和槽尺寸过小、而铸件壁厚较大时孔可不铸出,待机械加工时切出,这样可简化铸造工艺。一般铸铁件,φ<30mm(单件小批)、φ<15mm(成批)、φ<12mm(大量);铸钢件,φ<50mm(单件小批)、φ<30mm(成批)的孔可不铸出。
(5)芯头
芯头是指砂芯的外伸部分,它不形成铸件的轮廓,只落入芯座内,用以定位和支承砂芯腔。
(6)铸造圆角
制造模样时,壁的连接和转角处要做成圆角,便于造型、并可减少或避免砂型尖角损坏。但分型面的转角处不能有圆角。一般内圆角半径可按相邻两壁平均厚度的1/3~l/5选取;外圆角半径可取内圆角半径的一半。
4)铸造工艺图绘制举例
铸造工艺图有两种绘法。单件小批生产时,可直接在零件图上绘制,供制造模样、造型和检验使用;在大批量生产时,可另绘铸造工艺图。铸造工艺符号及绘制方法可参阅JB2435—1978。
铸件图
铸件图是反映铸件实际尺寸、形状和技术要求的图样,是铸造生产、铸件检验与验收的主要依据,也是机械加工工艺装备设计的依据。铸件图应在完成了铸造工艺图的基础上画出,用图形、工艺符号和文字标注。内容包括:切削加工余量、零件实际尺寸、不铸出的孔槽、铸件尺寸公差、硬度、不允许出现的铸造缺陷、检验方法及相关的铸造工艺符号等,右图是根据右上图的铸造工艺图绘制而成的铸件图。
九、铸件的结构工艺性
铸件的结构工艺性是指所设计的铸件结构不仅应满足使用的要求,还应符合铸造工艺的要求和经济性。合理地设计铸件结构,可达到工艺简单、经济、快速生产出合格铸件的目的。
1)铸件的外形
铸造工艺图是利用各种工艺参数及符号表示铸型分型面、浇冒口系统、浇注位置、型芯结构尺寸、控制凝固措施(冷铁、保温衬板)等内容的图样。他是制造模样、模板、铸型、生产准备和验收最基本的工艺文件。
(1)外形力求简单平直。尽量采用规则的易加工平面、圆柱面等,避免不必要的曲面、内凹等以便于制模和造型,简化铸造生产的各个工序。
(2)避免或减少活块。合理设计零件上的凸台、肋板,厚度应适当、分布应合理,以方便起模。右图a上的凸台一般要用活块才能取出模样;若采用右b结构,将凸台延伸,可采用简单的两箱造型,避免了活块。
(3)尽量减少分型面的数量。分型面少且为平面可避免多箱造型和不必要的型芯,不仅可简化造型工艺,还能减少错型和偏芯,提高铸件精度。右图为底座铸件,若采用a结构,需采用三箱造型或外芯辅助造型,工艺复杂;若将其外形改进为b结构,则可采用简单的两箱造型。
(4)应设计结构斜度。在垂直于分型面的非加工面应设计适当的结构斜度,以便于起模,避免在起模时损坏型腔,提高铸件精度。一般手工造型木模的结构斜度为1°~3°。铸件垂直壁的高度增加,结构斜度减小;内壁的斜度大于外壁的斜度;木模或手工造型的斜度大于金属模或机器造型,有结构斜度的内腔,有时可采用吊砂或自带芯子。下左图为结构斜度示例。
(5)避免收缩受阻。铸件的结构应利于自由收缩,以免产生较大的铸造内应力,防止铸件开裂。下右图为轮辐设计方案,a方案采用偶数直轮辐,虽然制模方便,但铸件收缩受阻,易在轮辐处产生裂纹;若改为b或c方案,收缩时可借弯曲轮辐或奇数轮辐轮缘的微量变形减少铸造内应力,防止开裂。
(6)避免过大水平面。过大的水平面不利于金属液的填充,易产生浇不到和冷隔;不利于排除气体和夹杂物;在大的水平面上方,铸型受金属液的烘烤易开裂使铸件产生夹砂缺陷。将大的水平面改为倾斜面,可防止产生上述缺陷。
2)铸件的孔和内腔
(1)尽量少用或不用芯。铸件上的孔和内腔是用型芯来形成的,其数量的增加会使生产周期延长,成本增高,并使合型装配困难,降低铸件的精度,容易引起各种铸造缺陷。右图为悬臂支架的设计,a图是中空结构,需要用一芯来铸出,改进后b图为开式结构,可不用芯子,这样简化了铸造工艺。
(2)有利于芯的固定、排气和清理,防止产生偏芯、气孔等缺陷。下图a为轴承架铸件,结构的内腔要用两个芯形成,其中较大的为悬臂芯,装配时要用芯撑来支承,芯子的固定、排气和清理都困难。改进后的b结构只用一个整体芯,下芯方便,且排气和清理容易。
3)铸件的壁厚及壁间连接
(1)铸件的壁厚应合理
铸件的壁厚应保证力学性能,便于铸造生产。铸件的壁不能太薄,否则会受金属流动性的影响,产生浇不到、冷隔等缺陷。铸件的壁厚也不宜过大,否则会在壁的中心处形成晶粒粗大,产生缩孔、缩松等缺陷。每一种合金都有一个临界壁厚,当铸件的壁厚超过这个尺寸后,铸件的承载能力并不是按比例随之增加。铸造合金的临界壁厚可按其最小壁厚的三倍来考虑。为保证铸件强度和刚度,可在铸件的脆弱处增设加强筋。
(2)铸件的壁厚应均匀
铸件各部分壁厚相差过大,不仅容易在较厚处产生缩孔、缩松缺陷,还会使各部位冷速不均,铸造内应力增大,造成铸件开裂。右图为使铸件壁厚均匀的设计例子。
(3)铸件的壁间连接应合理
转角处应有结构圆角。如右图所示,a图铸件直角转角处金属积聚,易产生缩孔,内侧转角处应力集中严重,易产生裂纹。b图采用结构圆角过渡可避免上述缺陷。
避免交叉和锐角连接。铸件壁的交叉处热量蓄积较多,易形成缩孔和缩松,因此要避免交叉。对中小型铸件可采用交错接头,大型铸件可用环状接头。铸件壁间连接如出现小于90°的锐角,可采用过渡形式。见下左图,a结构比b结构合理。
应避免壁厚突变。有时铸件的壁厚不可能完全一致,厚壁与薄壁的连接应采用逐渐过渡,以避免因壁厚突变而引起应力集中。下右图为薄厚壁的逐渐过渡形式。
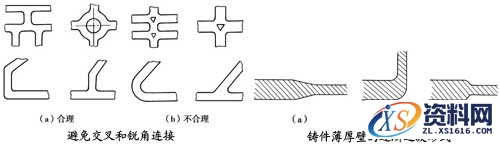
1;所有标注为智造资料网zl.fbzzw.cn的内容均为本站所有,版权均属本站所有,若您需要引用、转载,必须注明来源及原文链接即可,如涉及大面积转载,请来信告知,获取《授权协议》。
2;本网站图片,文字之类版权申明,因为网站可以由注册用户自行上传图片或文字,本网站无法鉴别所上传图片或文字的知识版权,如果侵犯,请及时通知我们,本网站将在第一时间及时删除,相关侵权责任均由相应上传用户自行承担。
内容投诉
智造资料网打造智能制造3D图纸下载,在线视频,软件下载,在线问答综合平台 » 砂型铸造工艺过程