近年来,诸多学者针对回弹补偿方法进行了大量研究。王发成等采用Dynaform软件对某叶片进行冲压成形模拟和回弹计算,并借助回弹补偿模块,采用有限元方法预测回弹量并进行相应的回弹补偿。聂昕等采用型面整体变形算法对汽车梁类零件的型面进行回弹补偿,该方法能有效提高回弹补偿效率,且具有高精度和补偿准确的特点。冯杨等提出了一种基于补偿因子的模面修正方法,该方法将零件的型面分成多个截面,在各截面上实施不同的补偿因子,以提高型面补偿精度。Sheu等提出采用双弧曲面模型(Bi-arc surface model)对扣描的冲压件的点云数据进行逆向建模.并以此对模具进行同弹补偿。
现有研究主要集中在形状简单或者零件本身具有基准平面和基准孔的零件。然而,针对复杂曲面零件回弹补偿的研究较少。本文以某大型核电汽轮机空心叶片外弧为例,提出采用三维扫描仪对冲压成形的叶片零件进行三维全型面检测,通过进行逆向建模得到扫描模型,并与设计模型进行对比得出实际回弹量,采用逆向数据进行准确的回弹补偿。
1 三维全型面检测方法
图1为某大型核电汽轮机空心叶片外弧零件的三维图。该零件的制造工艺为落料、热冲压成形、激光切割、焊接(与内弧零件)和二次激光切割。图1所示叶片外弧有11个平行的截面(C1~C11),实际生产中将零件放置在具有11个相同截面尺寸的专用枪具上。采用间隙尺测量实际零件与截面的偏差量。本文所研究叶片外弧零件的截面绝对偏差小于等于1.5mm。
图1 空心叶片外弧零件
在对零件尺寸是否合格的评判方面,采用传统检具的截面检测方法具有较高效率,但对于不合格的零件,需要对模具型面进行回弹补偿,采用传统检测方法进行回弹补偿十分麻烦。由于叶片的型面复杂,传统的检具检测化置有限,且利用检测数据进行建模修改麻烦,导致对模具模面补偿的过程十分耗时,且准确度不高。针对类似的具有复杂曲面的零件,本文提出采用三维全型面扫描的方法来检测零件,其检测流程如图2所示。
图2 三维全型面扫描检测方法
首先对零件进行门描前的预处理(包括表面清理、喷涂显影利和贴标识点)。考虑到该零件为复杂曲面,没有任何特征面和特征孔,通常情况下对此类零件后续对齐常常采用手动对齐和最佳拟合对齐,这些方法对齐误差较大,对结果影响大。针对这类复杂曲面零件,本文提出将零件放置在模具上,在模具上选定基准,将零件和模具上的基准的所有数据都进行扫描和记录,便于后续对齐比较,减少了对齐误差。扫描检测中选择图3(a)所示的3个基准平面作为后续的对齐基准平面。
图3(b)为试验采用的三维全型面扫描设备,该设备为Shining 3D-Scanner系列三维扫描仪,型号为EaScan-D,产于中国浙江,其扫描精度为0.02 mm。该设备为非接触式三维扫描方式,扫捕过程对被检测物体没有损伤,主要应用于产品设计开发、逆向工程及工件检测。本文借助该设备对复杂叶片外弧零件连同模具上的基准一起进行扫描,计算机可以获得扫描后的点云数据。通过逆向建模软件对得到的点云数据进行处理(包括点云对齐、采集、降噪、封装、填孔和修补等操作),得到扫描后的片体模型。最后,将模具上对齐的基准平面和外弧零件的设计数模导人,用于与扫描模型的对齐和二维比较。通过三维比较可以得到三维扫描零件与实际设计模型的偏差量,该方法还可以用于分析零件孔位位置、孔位直径、零件各边回弹偏差量等。此外,三维全型面扫描的逆向建模数据还可用于 弹补偿和机械加工等。
图3 扫描基准和使用扫描设备
2 三维全型面检测结果
采用前面提出的方法对零件和模具上基准面进行三维全型面扫描,并用与没计数模进行比较。比较过程中基于模具上的3个基准平面进行对齐,3个平面对齐误差分别为0、0.017和0.018mm。图4为叶片外弧的三维比较偏差图。由图4可以得出:该零件的最大正偏差为2.59 mm;最大的尺寸负偏差为-3.04 mm。各个截面的二维截面偏差量可以通过截取截面查看,从左到右的l1个截面中,截面C2、C5、C6的最大绝对偏差值小于1.5 mm;其余截面部分区域超过了1.5mm。即零件尺寸偏差过大。图4(b)为C8截面的二维尺寸偏差量。
图4 叶片外弧三维比较的偏差图
通过扫描数据进行逆向建模,一方面可以用于评价零件的三维和二维的偏差量;另一方面还可以用于模具型面的回弹补偿。首先,导入三维扫描模型以及原始零件数模;然后,利用回弹补偿算法反箅出回弹补偿面;最后,利用所得到回弹补偿数据加工模具。
3 基于逆向工程的回弹补偿
图5为本文采用的基于扫描数模的回弹补偿示意图。假设本文所研究的零件是由”个节点组成的有限元网格集合R³。图5(a)中所示数模满足以下关系:
节点;n为零件节点总数;a为补偿因子,补偿因子a通常为负值,其值为-2.5~-1.0,与材料的性能和厚度有关。
图5 基于扫描数模的回弹补偿示意图
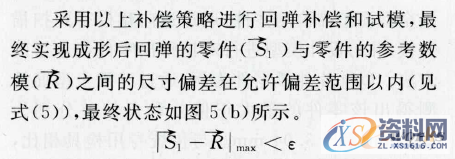
图6 基于逆向工程的回弹补偿流程图
图7 回弹补偿结果
4 试验
采用逆向工程数据进行问弹补偿的型面可用于直接加工模具。试验中零件的扫描模型和对比参考数模均为零件的上层片体模型, 此补偿数模用于直接加工模具的凹模型面,凸模和压边圈的模具型面需偏置一个料厚进行编程加工。由于叶片外弧零件的拉延成形设备为常规薄板成形液压机,零件的成形由工人操作,因此对馍具的闭合高度没有严格尺寸要求。 在回弹补偿后,对模具进行二次加工,加工编程过程中,以现有模具刑面状态作为待加工的原始状态,以回弹补偿型面作为目标型面状态,借助UG软件加工编程模块,采用整体最小加工量进行数控力加工编程。图8(a)(b)(c)为试验中加工的叶片外弧热成形模具。
图8 试验模具和线切割后的零件
试验步骤:① 将板料放人电阻炉中加热到870℃,为保证板料内外部加热均匀且不发生过烧,达到没定温度870℃后再保温6 min;② 试验中采用水基高分子和石墨乳作为润滑剂,均匀地涂缀在模具型腔和压料面上;③ 从加热炉中取出板料并快速转运到模具上,整个转运时间控制在17~22 s内。以保证板料不至于降温太多;④ 压机下行,对板料进行热冲压成形;⑤ 凸凹模闭合后,保压7.5 min;⑥压机上行,取出成形后的叶片背弧零件;⑦ 将叶片放置在空旷位置,冷却至室温。
对得到的热成形叶片外弧零件进行激光切割,得到零件如图8(d)所示。采用前面提出的三维全型面检测方法对该零件进行检测,利用Geomagic Qualify软件对扫描模型以及设计模型进行3D尺寸偏差比较,得到如图9所示的回弹补偿后叶片外弧三维比较偏差图。图10为各个截面凹弹补偿前、后的最大偏差值。从图10中可以看出:该叶片外弧的最大正偏差为1.36mm;最大的尺寸负偏差为-1.43 mm,其绝对值均小于1.5 mm,满足叶片外弧尺寸偏差要求。
5 结论
(1)针对复杂曲面类零件提出了一种采用三维全型面扫描检测零件,通过逆向建模得到扫描数模,并与设计模型进行对比得出零件偏差量的方法。以叶片外弧零件为例,通过三维全型面检测得出该零件的最大正偏差和负偏差分别为2.59mm和-3.04 mm。与传统专用检具相比。三维全型面检测可以用于快速、全面地检测各类复杂零件,具有检测数据全和精度高的特点。
(2)针对常规复杂曲面零件偏差比较方法中对齐误差大的问题,提出将零件放置在模具上,在模具上选定基准,将零件和模具上的基准的所有数据都进行扫描和记录,便于后续对齐比较,减少对齐误差。
(3)采用扫描数据进行逆向建模,并用于对模具型面进行回弹补偿,提出基于逆向工程对复杂曲面零件进行回弹补偿的方法。对叶片外弧零件进行回弹补偿后,进行模具加工和试验,得到最终叶片外弧零件的最大正偏差为1.36mm;最大负偏差为-1.43mm,均小于1.5mm,满足叶片外弧尺寸偏差要求。
KN95口罩耳带机现货、N95切片加内置鼻梁一体机、N95口罩机整套现货,厂家直销没有中间商,预订电话:13018639977
CNC数控编程培训、塑胶模具设计培训,冲压模具设计培训,精雕、ZBrush圆雕培训、Solidworks产品设计培训、pro/E产品设计培训,潇洒职业培训学校线下、线上网络学习方式,随到随学,上班学习两不误,欢迎免费试学!
联系电话:13018639977(微信同号)QQ:2033825601
学习地址:东莞市横沥镇新城工业区兴业路121号-潇洒职业培训学校
1;所有标注为智造资料网zl.fbzzw.cn的内容均为本站所有,版权均属本站所有,若您需要引用、转载,必须注明来源及原文链接即可,如涉及大面积转载,请来信告知,获取《授权协议》。
2;本网站图片,文字之类版权申明,因为网站可以由注册用户自行上传图片或文字,本网站无法鉴别所上传图片或文字的知识版权,如果侵犯,请及时通知我们,本网站将在第一时间及时删除,相关侵权责任均由相应上传用户自行承担。
内容投诉
智造资料网打造智能制造3D图纸下载,在线视频,软件下载,在线问答综合平台 » 逆向工程的复杂曲面冲压件回弹补偿方法